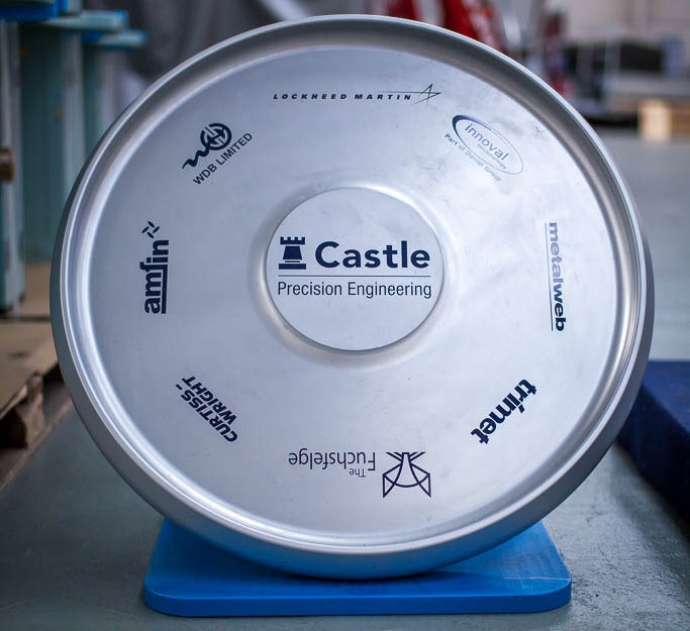
BLOODHOUND’s high-speed desert wheels each weigh 95 kilogrammes. They not only have to carry the weight of a 7.5-tonne car, but also must not fall apart when spinning at over 10,000rpm and subject to a force of 50,000g at the wheel rim.
What does that 50,000g mean? It’s the equivalent of saying that something sitting on the rim that weighs the same as bag of sugar when the wheel isn’t moving would weigh as much as a full loaded articulated lorry when it’s spinning at full speed.
In addition, the shape of the wheels – and in particular the rim – is very important as they must not sink into the surface of the desert at Hakskeenpan but need to have sufficient grip to avoid the Car sliding all over the surface.
Making 1,000mph wheels
The desert wheels were forged using well understood, mature manufacturing processes and high performing aerospace materials that are proven to work well.
After much testing, the material chosen for the wheels is a special alloy of aluminium mixed with zinc known as ‘7037’.
The billets that will eventually become the wheels were forged in Germany by Otto Fuchs using 6 tonnes of pure liquid aluminium delivered by Trimet. Forging breaks down the crystalline structure of aluminium, making it denser and stronger than if the wheels were made from cast aluminium. In the forging process the aluminium was heated to more than 390°C, moulded into discs with a 3,668 tonne hot press and then a 20,000 tonne cold press to produce a simple round (but large) ‘cheese’ shape. See BLOODHOUND TV Episode The Fastest Wheels in History.
The next stage was for each wheel to be milled into the final design by Castle Precision Engineering in Scotland. Each wheel weighs around 95kg each and has a diameter of around 910mm.
Stress testing
It’s one thing to make BLOODHOUND’s wheels but it’s another to determine whether they will perform in the real world just as predicted by our virtual tests (which used finite element analysis). To check this, the first wheel to be manufactured was ‘spun’ at 175 ‘spins per second’ on a test rig in Derby by sponsor Rolls Royce in 2014.
In this test we measured thermal and centrifugal expansion. The test was a great success and proved that the manufacturing process had been a triumph.
An interesting side effect measured in the spin test was that the wheels grew 0.8mm due to the load and another 0.35mm due to the heating effect at such high speeds. This is discussed in more detail by Andy Green in one of his diary entries.
Machining
Fifteen desert wheels were forged. From each batch we cut up one to validate the forgings, leaving 13 to be used for the Car.
One was machined to the final shape for the stress tests, with a further eight being machined for runs in South Africa in 2015 – giving us a main set, a second set and one spare wheel. The final four wheels will be left uncut so that the design can be tweaked after the first year’s desert runs, if necessary.
The wheels are machined to tolerances of just a few microns (thousandths of a millimetre). This is vital as otherwise there could be an imbalance as the wheel spins which causes a vibration and therefore a force on the axle, potentially wearing out or even destroying the bearing or other components.
Balancing
Once the wheels have been machined, they are sent to be balanced, just as you need to have your road car wheels balanced. However, if BLOODHOUND’s wheels aren’t balanced, the solution is not to put small lead weights on the rim but instead to finely revise the machining.
Non-destructive testing
After machining, each wheel will go through non-destructive testing (NDT).
In simple terms, this involves spraying the wheel with ultra-violet dye, washing this off with solvent, then spraying it with white developer. The wheel is then put it under a UV light to show any cracks or damage – the dye gets stuck in the cracks and the developer makes this show up under the UV light. This lets us make sure there are no nasty cracks in any of the wheels.
Why is this important? Because even though the desert runway has been cleared of rocks down the size of a pea, there are still bits of grit on the desert floor which, when kicked up by the front wheels at 1,000mph, will be hitting the back wheels with tremendous force. If they cause even a minute crack in the wheel, we don’t want that crack to spread.
Shot peening
The next stage in the process of making a desert wheel is ‘shot peening’.
Machining creates expansive forces in the skin of the wheel, so that this skin is always trying to expand. This means that if a crack is caused by something hitting it very hard, those forces may cause the crack to propagate.
The solution is to use shot peening, where the surface is hit hard enough with tiny steel shot to cause it to deform and produce a very thin layer with a compressive force in it instead. Now, if anything hits it, the crack won’t try to tear itself apart any more.