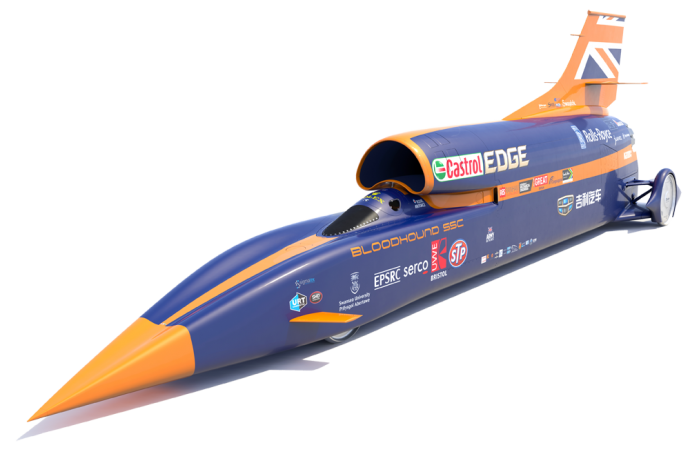
BLOODHOUND SSC is a hybrid construction because there are different requirements for the two ends of the Car. The front section of the Car (which consists broadly of the nose and the cockpit) is primarily made of carbon fibre composite while the rear section is made from metal.
Each part of the structure presents its own challenges in terms of design and manufacturing.
Forward structure
The front section of the Car consists of a carbon fibre monocoque, similar in concept to a Formula 1 tub. This provides Andy Green, our driver, with a very secure, rigid safety cell. It is also the most efficient way to form the complex curved design of the Car in front of the cockpit and main jet engine intake.
The monocoque needs to take the aerodynamic load (air pressure) of up to 10 tonnes per square metre. As a result, it has taken more than 10,000 hours to design and manufacture.
It is made from five different types of carbon fibre weave and two different resins. Sandwiched between the layers of carbon fibre are three different thicknesses of aluminium honeycomb core (8, 12 and 20mm), which provide additional strength. At its thickest point the monocoque comprises 13 individual layers but is just 25mm in cross section. Overall the monocoque weighs 200kg.
The monocoque bolts directly to the metallic rear chassis.
As a safety check, we’ve shot projectiles at the ballistic panels that will go on the side of the monocoque to ensure Andy will be fully protected from stones or other debris hitting the car at high speed.
Read more about:
Rear structure
The rear of the Car is a metallic structure that’s been constructed separately as upper and lower halves.
Upper chassis
The upper chassis houses the Eurojet EJ200 engine and the intake duct, and above this sits the fin. This half of the chassis is a ‘rib and stringer’ construction, similar to that used in the aerospace industry. The ribs are machined from aluminium billet and the stringers that run the length of the structure are made from titanium. The outer skin is also titanium in order to reduce the weight at the rear of the Car but keep it stiff.
The titanium skin was both glued and riveted on to the ribs – a process that used 11,500 aerospace rivets. It was then ‘cooked’ in a giant autoclave (effectively a huge pressure cooker) at the National Composite Centre to ‘cure’ the glue, in a process that saw the temperature raised by 5°C per minute, then baked at 175°C for one hour and allowed to cool overnight. Using both glue and rivets makes the upper chassis doubly strong, as either would be strong enough on its own.
Lower chassis
The lower part of the rear structure houses the auxiliary power unit, the jet fuel tank and the rocket system. It is made of a series of aluminium frames and bulkheads that are skinned in steel, using around 4,000 rivets to hold it together.
The furthest back portion of the lower structure forms the ‘rear subframe’. The rear suspension is mounted on this, together with the rocket thrust ring - which transfers the thrust of the rocket into the chassis – and the parachute cans and attachment.
Underside
The underside of the front of the Car – the monocoque – is titanium, while the floor of the rear of the Car is made of steel plate. Both materials were chosen to prevent the bottom of the Car from being worn through by the desert silt.