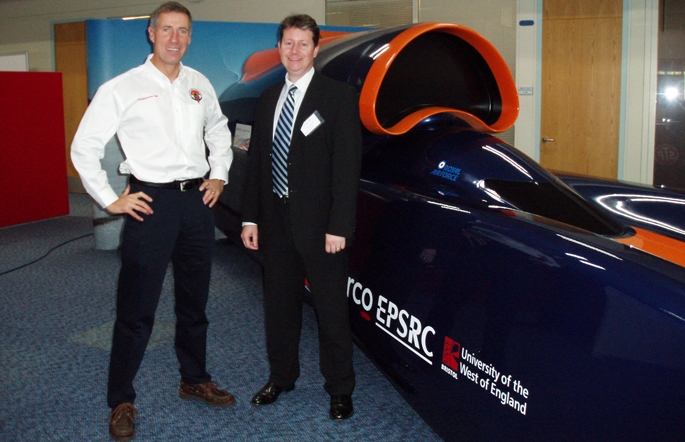
In the first of a regular series of articles about our sponsors, we hear from Innoval Technology – one of the BLOODHOUND Product Sponsors working on the Car’s desert wheels – about why and how it is involved in the Project. Innoval also explains how you choose the right materials for such hard-working wheels and what’s going to happen next….
Innoval – providing aluminium expertise to BLOODHOUND
Innoval Technology provides high quality consultancy and technical support to investors, manufacturers and end-users of aluminium across a broad range of industry sectors. Basically, we’re a group of aluminium experts! We know all about how the material is processed and the products it goes into.
Aluminium is the material of choice for many parts of BLOODHOUND SSC, from the Car’s wheels to large sections of its chassis and subassemblies. As such, Innoval believes the Project provides a powerful means of showcasing the technical capabilities of aluminium. We’re also passionate about inspiring the next generation of scientists and engineers.
For these reasons, we chose to become a BLOODHOUND Product Sponsor, which means we’ve been helping with the design and build of the Car, and in particular the desert wheels.
Who are we?
Dr Tom Farley, Innoval’s Managing Director, with Richard Noble, BLOODHOUND’s Project Director
Innoval is based in Banbury, Oxfordshire and we’re owned by equipment manufacturer Danieli. With our expertise in aluminium, we do a lot of work in the automotive sector. Our expertise covers metallurgy, surface treatment, lubrication, coatings and equipment engineering.
Aluminium plays a key part in this exciting and ground-breaking project, and Innoval is very proud to be supporting the BLOODHOUND adventure.
How are we involved?
The companies which make up the Wheel Consortium
Innoval Technology is part of BLOODHOUND’s Wheel Consortium. This is a group of nine companies who have worked together over the course of several years to design, manufacture and test BLOODOUND’s desert wheels, which are made from an aluminium alloy.
Right at the start of the Project we helped the team at Lockheed Martin – which conducted the initial feasibility study – to decide which alloy to use. The original alloy choices were AA2014 and AA7075, as these are the aluminium alloys used for aircraft wheels. They have also been used for earlier generations of land speed vehicles.
The two alloys were assessed for impact resistance by firing particles of material from the run site (Hakskeen Pan, South Africa) at very high speeds at alloy samples and looking at the nature of the damage caused by those impacts.
The ‘gas-gun’ trials were undertaken at the Cavendish Laboratory in Cambridge under the watchful eyes of the Lockheed Martin team. The trials investigated the damage introduced by the impact of rock particles at approximately 1,000mph.
The team conducted 10 experiments, five on each aluminium alloy. There was no sub-surface damage in any of the samples, which suggests that both aluminium alloys responded to impact by ‘plastic flow’ only – this means they didn’t crack, bend or break at the points of impact. However, to be conclusive, we needed a more detailed metallographic analysis, so we took several samples back to Innoval’s test labs for further analysis.
Testing using optical metallography
Optical microscope image of an aluminium plate from one of the impact damage trials.
We wanted to determine if any microstructural differences between the two materials could be observed after impact, and whether this could be used to rank the materials.
We used ‘optical metallography’ – which is where you use an optical microscope to study a metal’s structure – to examine the projectile impact area to look for evidence of ‘micro-cracking’.
As metals are reshaped or 'worked' they become harder. This is because of microscopic changes in the crystalline structure which take place within the metal as it is manipulated. We call this 'deformation hardening'. In the case of the BLOODHOUND test samples, when one of the projectiles hit an aluminium sample it made minute dimensional changes in the surface that made it harder, which we measured using something called ‘Vickers microhardness (Hv) measurements’.
In the regions where the projectile had hit the alloy, there was some tearing of the aluminium surface, but we found no significant cracks. The subsurface region was hardened by around 5-10% to a depth of about 1mm below the impact crater.
There were no significant differences between the behaviour of the two aluminium materials (AA7075-T651 and AA2014A-T651). As a result, the stronger AA7075 alloy was selected.
Seeking a stronger alloy
One of BLOODHOUND SSC’s aluminium wheels
Following the impact trials, the BLOODHOUND design team asked us if stronger aluminium alloys were available. We found that both Alcoa and Otto Fuchs had developed stronger alloys for large aircraft forgings, both of which were developments from the alloys AA7010 and AA7050. These, in turn, were developments from the original AA7075 alloy composition. The new alloys had the registered designations of AA7085 (Alcoa) and AA7037 (Otto Fuchs).
Both alloys had similar properties and were eminently suitable for making the BLOODHOUND wheels. However, the AA7085 alloy was not available in Europe, so the AA7037 alloy became the obvious choice. Furthermore, Otto Fuchs could produce the large diameter forgings suitable for manufacturing the desert wheels.
The wheels for the runway trials were made from the AA7075 alloy, because these did not have such a high strength requirement and so could be machined from blocks, not forged.
What’s next for us?
Our Materials Testing department will carry out a detailed analysis of the forged and machined AA7037 alloy wheels after the first desert runs. However, Innoval’s involvement with BLOODHOUND doesn’t stop there. Dr Timothy Clemson , one of our Process Engineers, is a BLOODHOUND Education Ambassador , supporting the Education Outreach team and bringing BLOODHOUND alive for children across the UK.
A testament to teamwork
BLOODHOUND’s Wheel Consortium is a great example of how teamwork between a group of companies can achieve great things.
We’re delighted to see aluminium play a significant part in the BLOODHOUND story, and we’re very proud to be involved. We displayed one of the demonstration wheels on our stand at a large aluminium show recently and it generated a huge amount of interest.
BLOODHOUND Ambassador Timothy Clemson explaining about the wheel