Wheel testing at Hakskeenpan
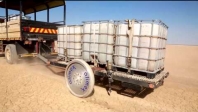
BLOODHOUND's wheels will be the fastest in history, they will be the only point of contact between this 135,000 hp jet and rocket powered car and the South African desert. Getting their shape right is crucial.
BLOODHOUND's wheels will be the fastest in history, they will be the only point of contact between this 135,000 hp jet and rocket powered car and the South African desert. Getting their shape right is crucial.
Cisco Bloodhound TV visited product sponsor Otto Fuchs in Germany to see the first stage of the 1000mph wheels being forged from aluminium
Last week I was in Singapore, for a forum on Innovation, Technology and Design. The British Council and the British High Commission had invited an A-list group of UK companies to showcase the best of British expertise. It was an impressive list, including McLaren, Rolls-Royce, Arup, Dyson – and BLOODHOUND.
Ron Ayers and Brian Coombs visit Hakskeenpan to try out the wheel design on the surface. The wheels are attached to a trailer called "Mad Max"
Lockheed Martin UK is providing Research & Development in the first step towards designing the wheels on the world’s fastest car, BLOODHOUND SSC.
Lockheed Martin is leading a 700 hour ’wheel concept study’, to identify and explore initial ideas for the wheel design, which, made from premium grade solid titanium, will experience the most extreme driving conditions ever known:
The BLOODHOUND Project, Britain’s 1,000mph land speed record attempt, announced today that wheel bearing manufacturer Timken will be sponsoring the wheel bearing solution for the BLOODHOUND SSC (Super Sonic Car).
Timken has been working closely with the BLOODHOUND Project design team to produce a solution for the bearing challenge. Timken has already delivered the first three car sets of bearings for validation testing and runway tests and will continue to work closely with team.
This diary is my own look at the BLOODHOUND Programme as we try to build the world’s first 1000 mph Car – and, even more ambitiously, as we try to inspire a national interest in science in engineering. It’s a huge task, but worth the effort. If we want to live in a high technology low-carbon world in the near future, then someone is going to have to build it for us, and that someone needs to be inspired now.
by Andy Green
by Brian Coombs
The wheel is a very complicated component. It has to cope with very high loads applied to it, and has many other constraints imposed on its design.
When we started our design work, we did not know where we were going to be running, or even what the surface would be – salt as on Lake Eyre in Australia or playa as at Black Rock in USA. Our design was therefore based on the data we had from Thrust SSC and started with a wheel that was 900mm in diameter and 150mm wide, which we thought would have to be made of titanium.