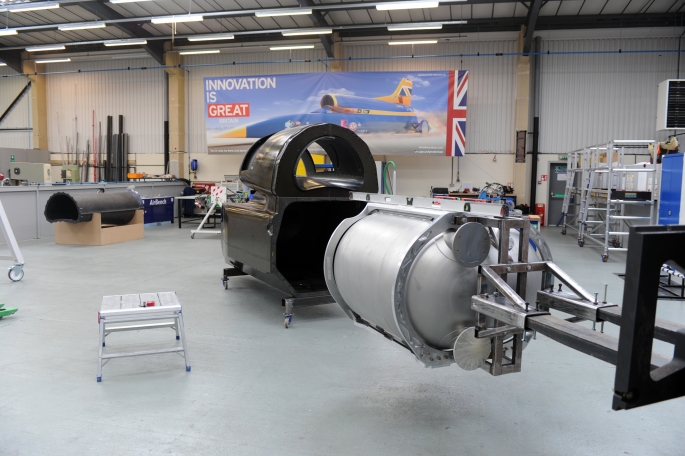
Picture above: Test fitting of the rocket fuel tank - a perfect fit!
It’s late in February as I write this update and the year is off to a flying start. The continued design release, manufacture and assembly of the components for BLOODHOUND SSC is progressing at great pace.
Rear Chassis
The titanium skins for the rear upper chassis crown sections are in place. The panel drill-off is starting to happen well ahead of schedule, which is great news. This is thanks to our great assembly team, Timet for the material, Amada for the punch and laser work, and GP Panelcraft which has done a great job of the 2D rolling of the skin sections.
GP Panelcraft has also made the 3D rearmost skins which are being collected as I write. These complex 3D curved panels, together with all the forward lower section 2D panels, will be trimmed and final fitted over the coming months. GP Panelcraft is better known for producing aluminium bodies for classic cars, but it has done a great job manufacturing the one-of-a-kind titanium skins needed for the most complex car in human history.
Fin structure
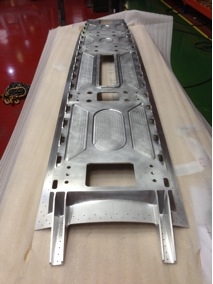
Another notable recent arrival is the most extreme machining we have produced so far… and the very good news is that it fits perfectly. The ‘fin shear plate’ fits to the rear upper structure and acts as the key interface between the upper structure and the fin. Consequently it needs to be perfect, as the fin position will only be as good as this interface allows. And as the fin is the hardest working fin at this low altitude in human history we were very keen to get it right! Manufax has done the most amazing job of what was a very challenging one-off part – it started as a solid billet of 750kg but the finished part weighs just 7.8 kg and has a wall thickness of just 2mm in many places.
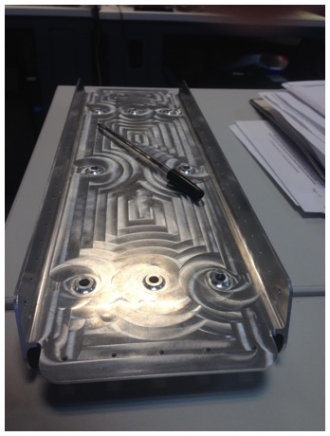
The fin structure itself has now been released to manufacture, with all the material sponsored by Smiths High Performance – thanks team! The huge leading edge and main spars will again be made by Manufax. These spars are large at the base and very fine at the tip. This change in size happens over less than two metres, which makes manufacturing these components challenging, but also very interesting.
The smaller intercostals which connect the spars in this aerospace design are being made by numerous motorsport manufacturing partners, who are used to making highly accurate one-off parts of this size. We have already made one to prove out the process and the good news is that it is spot on, so we can crack on and make the rest of them ahead of receiving the big spars.
We will be using a combination of soft tooling, using our Leica tracker care of Hexagon Metrology, and hard tooling, care of the huge fin fixture being built by Manufax. (Manufax created the fixturing which we have already successfully used in the lower chassis, rails and the side sections of the car.) This new fin fixture will also double up as the storage or stillage for the fin when it’s not fitted to the car itself and so it is being made in aluminium to keep its weight down for when it’s flown to South Africa separately from the car. We will use the Leica tracker again to realign the fin on the car before its first runs in the desert.
Front structure
The detailed design for the front structure of the car is underway and is progressing really well. We now have three new composite engineers working in this area and that extra resource will soon be bearing fruit.
We are currently finalising composite material choices for some of parts of the front structure of the car, in particular the high erosion areas. We are doing this with the help of SHD, our partner on composite materials and are about to test some candidate composite materials for these high erosion areas. SHD has taken great care to produce fully representative and accurate material samples for this trial – as always going the extra mile! These samples will undergo rigorous tests to see which of them will cope best.
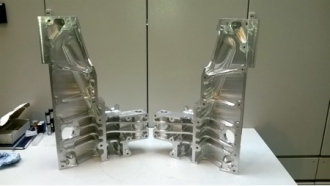
The front suspension sub assembly components continue to progress at AMRC. The four huge forgings sponsored by thyssenkrupp Materials are becoming four very large and highly detailed assembly elements which, when bolted together, will form the major structure upon which all the front suspension loads react. It is truly humbling to see the level of care and attention that the AMRC guys have put into this job so far and I’m really looking forward to seeing the finished articles bolted to the front of the monocoque later this spring.
HTP tank
The bespoke HTP tank, made by ABC Stainless, and carbon monocoque (produced by URT) came together this week for the first time. The monocoque is home to the tank and it’s fair to say it was always supposed to be a ‘snug’ fit. But that’s just what we want. BLOODHOUND SSC may be a 13 metre long car, but every mm of space counts.
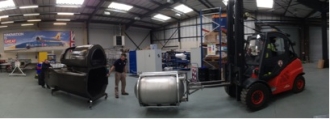
You can’t be too careful when manoeuvring two vital – and completely unique, one-off – components. We used the forklift (supplied by Linde) to hold the tank frame in position while the carbon monocoque was slide over it into place – and the good news is that it is a perfect fit! The planned packaging space above the tank is definitely snug, but the assembly team is confident it can reach everything as planned.
Spring forward…
2014 is a pivotal year for the BLOODHOUND SSC project, but I’m pleased to report we have made a great start and we are all determined to carry that momentum into the spring! Watch this space….