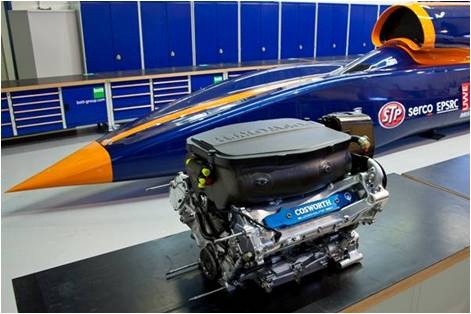
The engineering team remains hugely busy with the detailed design of the Car. We are still on course to start manufacturing the chassis next month, so there’s a real buzz in the BLOODHOUND Technical Centre down in Bristol.
Last month we announced that we’d be using a Cosworth F1 engine (pictured above) to drive the pump for our Falcon Hybrid Rocket. The engine will be mounted ‘backwards’ in BLOODHOUND SSC (when compared with a Formula 1 car), so it will have to produce 700 hp to drive the rocket pump under high G loads in the ‘wrong’ direction. One more technical challenge to add to the list – but at least we’ve got Cosworth’s expertise to help with solving this one.
The Cosworth engine will pump a tonne of HTP into the rocket in just 20 seconds, while accelerating BLOODHOUND SSC from 350 to 1000 mph – it’s going to be quite a ride! If you haven’t seen the Falcon Rocket in operation yet, have a look at the video of the Rocket test firing.
Test Firing our Falcon Rocket last year
Our education team continues to work hard, with more schools signing up to our Education Programme every week. I was able to join in last month, giving the Sir Isaac Newton Annual Schools Lecture at the Royal Air Force College, Cranwell.
I think Newton would have liked the physics of the Land Speed Record. Jet and rocket cars work using Newton’s third law of motion: ‘Every Action has an Equal and Opposite Reaction’ – in other words, the jet/rocket blast from the back of the car pushes it forwards, and more jet blast equals more speed. Slowing the car down is Newton’s first law: ‘A vehicle continues in a straight line at constant speed unless acted on by an external force’ – so we need airbrakes and drag chutes to provide enough ‘external force’, to stop the Car running off the end of the track.
The latest airbrake model
The airbrake design is coming on well – the results from last month’s computer modelling showed that the ‘perforated’ airbrakes give more drag and less vibration than solid panels – so this is what we’ll use.
The picture also shows the lower tailplane and larger fin shapes that we’re testing. We need the larger fin to give the Car enough directional stability – the problem is that with a bigger fin, the loads at the back end of the Car increase. Hence the chassis needs to be stronger and heavier at the back, which moves the Centre of Gravity back – and means that we need an even bigger fin...
This vicious circle is our current aerodynamic problem, but we solved bigger problems than this, so I’m not too worried. And there is one obvious advantage to a bigger fin – more room for you to put your name on the Fin of BLOODHOUND SSC. Now’s your last chance to buy a unique present for Christmas 2010!
Neil Armstrong meets our ‘Rocket Man’ Daniel Jubb
We had a very special visitor at the BLOODHOUND Technical Centre in Bristol last month – Neil Armstrong. Our engineering team gave Neil and his party a detailed brief on the Car and its technology. At the end of the brief, Neil gave us a fascinating insight into his test pilot and astronaut experiences – and I’m delighted to say that he fully supported our step-by-step development approach with BLOODHOUND SSC.
Neil also gave us a perfect summary of BLOODHOUND’s engineering approach, in the form of a famous school-room question. ‘Two students, a young man and a young woman, are standing 10 metres apart. Every 15 seconds, the young man halves the distance between him and the young woman – so how long will it take for them to get together?’ The mathematician in the class immediately answers ‘Never – it’s an infinite series and they never actually meet.’ The engineer in the class thinks for a moment and then comes up with a different answer: ‘Two and a half minutes’. Why? ‘Because after two and a half minutes, they will be close enough for all practical purposes!’
This has to be the aim of BLOODHOUND’s engineering solutions – not perfect, but ‘close enough for all practical purposes’. Our huge thanks to Neil for his time and his encouragement in our race to 1000 mph.
The clearance work has started at Hakskeen Pan
Great news from South Africa – the Northern Cape team has started work on the world’s fastest race track. The huge task of clearing 24 million square metres by hand, plus removing the soil causeway at the north end of Hakskeen Pan, will take several months.
In order to help them as much as possible, we advertised for some extra help in the Times last month. ‘People wanted to clear desert track for 1000 mph racing car. No wages, constant heat, tough work in beautiful but remote Hakskeen Pan, Northern Cape, South Africa. Scorpions may be present. Inspiring next generation of engineers the reward.’
We’ve already had over 100 volunteers, with more still applying to come out with us early in 2011 to help clear the desert – come along and join us! Alternatively join our Supporters’ Club and come out to see the Car run in 2012. There’s never been anything like this before – ever.
The Gas Gun at Cavendish Laboratory – making stones into bullets
Despite all the effort to clear the desert, there is always the chance of the Car hitting small stones. If the front wheels throw up a stone, then it will hit the rear wheels with an impact speed of 1000 mph – the speed of a bullet. To find out what this would do, last month we used a gas gun to fire lumps of stone from Hakskeen Pan into samples of aluminium alloy.
The bad news is that the aluminium is not ‘bullet-proof’ – but that’s OK, as we can fit steel ‘mudguards’ in front of the rear wheels to protect them. Another problem solved, one step closer to 1000 mph.
Looking back, it’s been an amazing year. The major achievement of 2010 must be finding the aerodynamic solution that will get us to 1000 mph. On top of that, we signed up major Product Sponsors to make the chassis and to supply our F1 engines, and we launched our full-sized Show Car at Farnborough. The wheel profiles were agreed and tested, the Vehicle Technical Specification was published on the BLOODHOUND website and we now have well over 4000 schools and colleges signed up for our Education Programme. In South Africa, work has started on the world’s fastest race track.
We’ve achieved a huge amount in 2010, as the major design effort draws to a close. It’s almost 2011 – the year that we build the world’s fastest Car. Meanwhile, here’s wishing you a Merry Christmas and Supersonic New Year!