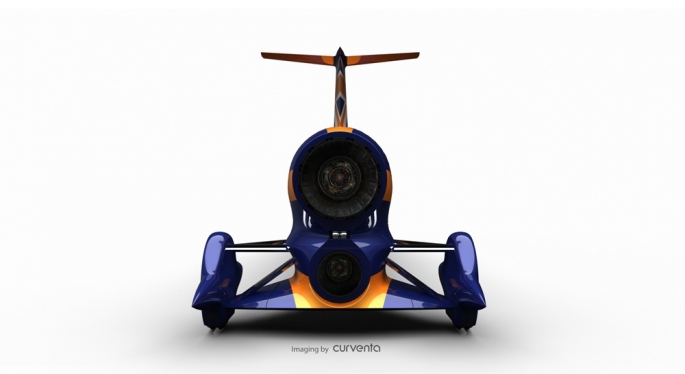
Project BLOODHOUND is making some real progress, which is an exciting feeling. We’re close to finishing off the final shaping at the back end of the Car and, after a lot of research and debate, we’ve also settled on the lateral stability requirement for the Car. It needs to resist a 0.8 G lateral load, which will give us a rear wheel track that is narrow enough to do 1000 mph, but plenty wide enough to make sure the Car doesn’t roll over. Both of these characteristics get my vote!
Our rocket expert Daniel Jubb and the pump impeller
Last weekend I saw the first manufactured component that will go on the Car. Of course, we already have the EJ200 jet engine that will power the Car, and we had the first set of wheel bearings delivered last year, but this is different – this is a piece designed and made specifically for BLOODHOUND. It’s the pump impeller, which will force a tonne of hydrogen peroxide (HTP) into the rocket in just 20 seconds. It seems hard to believe that it will take over 600 HP to turn this little paddle wheel (even spinning at over 10,000 RPM) – we need our 800 HP V12 engine in the Car to turn it!
I was down at the BLOODHOUND Technology Centre in Bristol last week, discussing how we will transport, service and refuel BLOODHOUND SSC once it’s ready to go. We also made some key decisions on systems, including the hydraulics, electrics, jet and rocket starting/shutdown, etc. Now I can get on with designing the cockpit in more detail – I should have a picture next month for you.
Moulding the steering wheel with Hywel
As part of the cockpit design, Hywel (one of our 2 year-in-industry students) has been given the task of designing the steering wheel for the Car. I need something easier to use than, say, an F1 car steering wheel, but with more controls than an aircraft steering yolk. Hywel is starting from scratch, taking a mould of my gloved hands to make sure that the wheel is a perfect fit for me. After a little trial and error (and without getting too much clay on his computer) we’ve now got a shape to scan and manufacture. Hywel’s loving the best year-in-industry job he could possibly imagine – you can read his side of the story here - and I can’t wait to see the fastest steering wheel in the world.
Another research programme that we started last year was to design a really good high-protection driver’s suit. Normal race suits only offer short-duration protection from fire (the cars are only going slowly – 200 mph – so they can stop quickly and jump out) and have never been tested against highly corrosive HTP (because they don’t have huge rockets attached!). Last year, Leeds University did some testing for us to show that a range of fire-resistant clothing can also withstand HTP, so now we’re looking for the most flame- and heat-resistant material.
A company called Lamination Technologies has developed an amazingly fire-resistant new material and is now doing some ‘Pyroman’ testing, which is showing great results. This is the sort of material that we plan to use for my driving suit and the team’s protective clothing. Not that I’m planning to set myself on fire, you understand, but just in case we have a problem – have a look at the scary video of the Pyroman testing below!
Pyroman test: Before, during and after a 12 second burn
It’s been a busy few weeks for presentations, on top of my full-time day-job with the Royal Air Force. The most fun events that we do are the 1K Club open days, showing our supporters’ club what we’re doing as it happens. For instance, they were the first people to see the rocket impeller (above) that will go on the Car. If you want to share this Engineering Adventure with the team, as it happens, then come and visit us. See you soon!