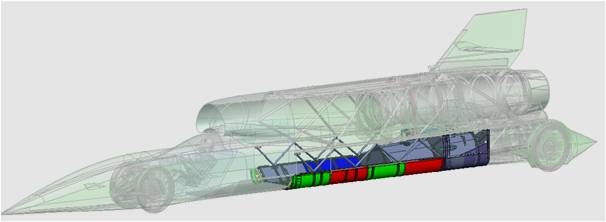
The service light blinking on my car this morning, serves to remind me that March was a busy month on the road again and I really should find a quiet moment to get it into the dealership for some TLC!! – March certainly moved at quite a pace!
Wigan was again on my visit list - It was great to see some of the larger lower chassis frames move from the programming stage and into production on the larger machining centres at Hampson BHW Wigan site and we are all working hard to keep programmes and material flowing from Thyssen Krupp into Hamspon to keep the machines turning. The lower chassis parts made by AMADA in Kidderminster are now relocated to the build area at the Hampson BHW Wigan site where the kit of parts for the lower chassis grows ever larger each time I visit.
On the composites build side, UMECO have had the release of surfaces for the carbon composite monocoque for the blocking up / tool design phase of manufacture, and as I write we’re only two weeks away from release of the final surface for the lower section of the monocoque. That deadline has the guys in the office working very hard to ensure Stuart Allen, our resident lead Engineer on composites, has all the details he needs on anything and everything that bolts onto that lower monocoque section. Making a prototype vehicle which is also the final operational version presents its own challenges and we have to be flexible in our approach to composites tooling. Ideally we want to avoid making additions or modifications to the tooling, but the reality is we need build in some flexibility so it’s less painful when we do. It’s very exciting to see the composites manufacture kick off properly and I look forward to seeing the design for the tooling and the male pattern for the lower monocoque develop over the coming weeks.
We are working with the Advanced Manufacturing Research Centre, AMRC, in Sheffield to complete some component testing. Myself and Mark Chapman our Chief Engineer were lucky enough to visit them in late March and were given a tour of the AMRC, the Nuclear AMRC, the new AMRC Composites centre and also the very comprehensive AMRC test facility. The day was rounded off with a session in their 3D Virtual Reality Cave where we were able to fly around a slightly older CAD version of the BLOODHOUND car, never the less it was a very remarkable experience and a very powerful tool to give us both a real world view of some of the areas of the car that are not yet detailed for manufacture. The AMRC is a true success story in its own right and is a very remarkable group of facilities. Thanks again to all the team at AMRC for making us feel so very welcome on our visit. More news on our work with AMRC later.
What do I think April will bring?: Well by the end of the month we’ll be kicking off the manufacture of the male buck for the lower monocoque and releasing the design scheme for the upper rear chassis to kick off the fixture design on that area. The kit of parts for the lower chassis will continue to grow and our emphasis will shift to planning for riveting and bonding the lower section together ready to get it clear of the fixture, so the fixture can go off to be modified ready to receive the upper chassis! We will also be kicking off on the design project for the Fin - more on all of that at the end of the month!
Thanks to all those companies that have taken the time to register their interest to be a supplier for the build of BLOODHOUND SSC on our website. We've had a great response, if you are a manufacturer and have not registered yet - then register to join our supply chain.