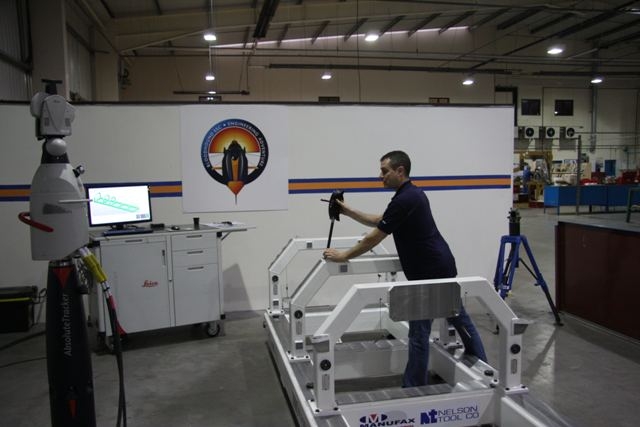
Manufax Engineering and its sister company Nelson Tool Company are delighted and excited to be part of such an engineering adventure as Bloodhound SSC. With a core business of supplying precision engineering tooling, jigs and fixtures to the Aerospace and other industries, we have over 60 years of experience or designing and building close tolerance tools for large structure assembly.
This is the story of how the tooling was developed ...
The tool design started with close collaboration with Hampson Aerospace and the Bloodhound team looking at the opportunities for Design For Manufacture, looking at how best to make the component parts and the best method of assembly of the Chassis. |
![]() |
At this early stage of design we worked with the designers to provide support in how the tooling needs to locate the components in the correct position, where best to put tooling holes and the overall concept for assembly. |
![]() |
The pictures shown on the right show the assembly concept and how the main elements of the structure are positioned and the rest of the components are fitted around them. This ensures that the final aerodynamic shape of the car is maintained. With this build design we will use a Laser Tracker to position the components and holes for drilling. The use of this technology will allow a fast accurate build to the exact Bloodhound car design. |
![]() |
Design Concept:
|
This is the first stage of any tool design. We take the information from working with the customer (Bloodhound team and Hampson Aerospace) on how to build the assembly. The concept is then agreed by the project partners and the design is then refined into a final tool design
The tool design then starts to take shape around the above build sequence. The tool design takes into account how to hold the parts while they are drilled and fastened together. Our tool designer looks at any areas that are difficult to access and where parts as a final assembly may clash with the tool. |
![]() |
The tool designer and engineering team here at Manufax and Nelson Tool then take the finished tool design and convert these into assembly and detail drawings. Our skilled toolmakers then take this information and use it to make the detail parts of the tool. From ordering the material, kindly supplied by Tata Steel, fabrication and machining of the structure to final assembly and laser tracking.
How an Assembly Fixture is made
![]() |
![]() |
Material supplied in long lengths from Tata Steel |
Material is cut to shape and welded together |
![]() |
![]() |
The welded fabrications are then machined to create flat surfaces and accurate positions for the holes and location points. |
Then the tool is assembled at the Manufax / Nelson Tool factory and painted |
![]() |
![]() |
We then use Laser Tracker technology to measure all the interface points on the tool to make sure they fit the CAD model of the tool. This tool is 6m long and all the points on the tool are accurate to 0.1mm. |
The fixture is then delivered to Hampson Aerospace in Wigan ... |
![]() |
![]() |
... and we install and re-measure the jig with a laser tracker to ensure the tool is still accurate and ready for build. |
|
The finished article (right)
|
|
Mark Davis
Manufax Engineering Ltd