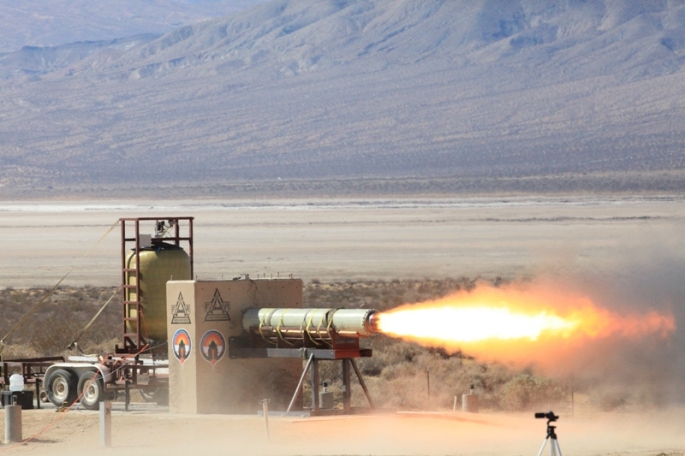
A successful static test of the 45.7cm (18-inch) hybrid was conducted on the 17th of October.
This is the first test of the 111 kN (25,000 lb) thrust chamber, which will be used on BLOODHOUND SSC. Good ignition was achieved and the chamber ran for 10 seconds, combustion was smooth. All hardware was in good condition after the test.
It was a relatively low pressure firing, the chamber was running slightly fuel rich.
As the test programme continues, we will increase the HTP delivery pressure and flow rate towards the design values of 75.8 Bar (1,100 lb/in2) and 47.6 kg/sec (105 lb/sec) respectively and the oxidizer:fuel (O:F) ratio will move towards our target. A network of thermocouples monitored the temperature of the motor casing and a number of pressure transducers recorded key values (such a chamber pressure).
The data is now being analysed, the chamber will be weighed to establish the mass of fuel consumed. The chamber will then be dismantled to enable inspection of the thermal insulation and to confirm the fuel grain regression rate.
“We now know that we can safely control a hybrid rocket to produce the required amount of thrust” said Daniel Jubb, BLOODHOUND SSC's rocket expert. “Now that we have completed the first firing we can commence with a rigorous programme of testing to refine the way the rocket burns. This is ground breaking science which will have applications in all areas of rocketry.”