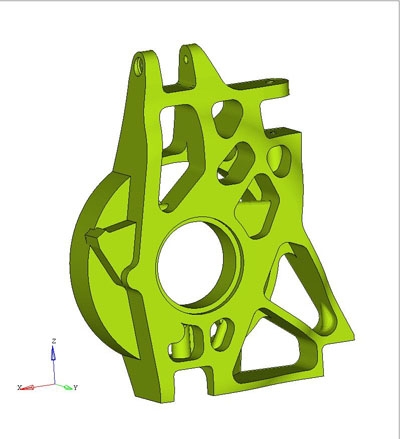
At a recent 1K Club engineering presentation, Mark Chapman talked about “Topology Optimisation” when designing parts of BLOODHOUND SSC. A grand sounding name, but what is “Topology Optimisation”?
Wikipedia says it is “a mathematical process whereby the location and number of voids within a structure is defined given a prescribed set of limitations and a clear objective”. Well, still not much clearer, so when I was at the UWE Design Office recently, I sat with Alessio D’Alesio, and he showed me exactly what he was doing.
The component pictured left is part of the rear wheel mounting – the wheel is attached to the central hole, and the suspension struts are attached to the four notches. Alessio programmed into his computer all the constraints on the component – for example, how much weight it has to bear and how stiff it needs to be when all the forces are applied to it at the various loading points throughout BLOODHOUND’s run profile. The Optimiser then analyses where the component needs to be strongest … and also where it doesn’t need to be as strong. These are areas where material can be machined away without affecting the overall performance.
The result of running the optimiser on his computer is shown in the picture on the right. The material that doesn’t add anything to the performance of the component has been taken away, leaving some surprising holes that just could not have been predicted. The component is then worked on some more by the design team and further optimised and eventually turned into the final design for the component which is pictured at the top of the page.
With this process being repeated for many of the car’s parts and even bodywork, the overall saving in weight will be quite considerable!
Nick Chapman