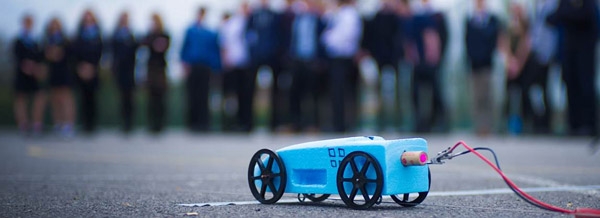
Engineering progress on the Project remains slow, as we focus our efforts on getting the funding together to run the Car next year. The good news is that we’re generating more and more interest, as global companies look at our fully-assembled Car and ask the question we want to hear: ‘How do I get involved?’. Putting global sponsorship packages together takes time, but thanks to the amazing Engineering Adventure that is BLOODHOUND, we’re getting there – watch this space.
What about steering it?
The extra time has given us the chance to develop our Education Programme (more of which in a moment). It also gives me more time to consider what BLOODHOUND SSC may be like to ‘operate’, which is pilot speak for ‘start up and drive’. Last October’s diary was a look at the proposed start-up procedures, which I’m still working on, as the Car’s systems and software will continue to develop over the next 12 months. I’ve also been reviewing the handling and stability of the Car’s design, which was summarised in last month’s look at the challenges of driving the world’s fastest car.
I say ‘possible’ challenges, as we won’t know for certain until we start running the Car next year. There is very little technical data on high speed steering with solid metal wheels. As a one-line summary of last month’s diary, it should be fairly easy to steer at slow speeds (up to 200 mph), rapidly becoming like driving on ice at 3-400 mph and then (probably) very twitchy at supersonic speeds. However, one thing I didn’t talk about last month was the possible effect of the solid wheels themselves, all rotating at high speed. In other words, driving a supersonic Car with a huge gyroscope on each corner.
Each of BLOODHOUND SSC’s wheels weighs 95 kg and will be spinning at up to 10,000 rpm. If you’ve ever tried rapidly spinning a bicycle wheel and then turning it, you’ll already understand the gyroscopic effect. The spinning wheel resists any movement and, if you force it, it will try to move in a direction at 90 degrees to the force you are applying (if this sounds weird, then take the front wheel off your bicycle and try it. It really is weird). The tendency to resist motion is called gyroscopic rigidity (or gyroscopic inertia), while the tendency to move at 90 degrees to the applied force is called gyroscopic precession. For a heavy disc turning very quickly (like a BLOODHOUND wheel), they are both powerful forces.
Power, not precession
In my day job in the Royal Air Force, gyroscopic effects can be very useful or very awkward. Gyroscopes in navigation systems enable precision navigation, but large high-speed rotating parts in an aircraft engine can be a real problem. In the early days of biplanes, many engines were ‘rotary’ engines, in which the whole engine rotated with the propeller, to help with cooling, etc. This caused huge gyroscopic precession effects: the rotary-engined Sopwith Camel biplane could turn right with ease but struggled to turn left.
Fortunately, this is not something that the RAF’s spectacularly agile Typhoons have to worry about. Their EJ200 engines (the same engine we’re using in BLOODHOUND) has low-pressure and high-pressure compressors that rotate in opposite directions, so there’s negligible gyroscopic precession.
If you’re trying to drive a Car supersonic in a straight line, then the gyroscopic rigidity helps to keep the Car pointing in the same direction, which is a good thing. However, while gyroscopic rigidity adds to stability, the gyroscopic precession is working 90 degrees out and, for high-speed driving, it’s not such a good thing. Any yaw movement, which could be due to a gust of cross-wind, or a steering input, will force all 4 ‘gyroscopes’ (wheels) to turn in the same direction as the Car. Gyroscopic precession, working at 90 degrees to the yaw force, will then try to roll the Car onto its side. This precession force is definitely not being a good thing.
A big gyroscope
Let’s consider how the Car might cope with this. The front wheels are one metre apart, with the rear wheels about 2.3 metres apart. This arrangement is designed to give the Car a high degree of roll-over resistance: the Car will only start to lift on one side if the side load roughly equals the weight of the Car. Since the Car weighs between 7 and 8 tonnes (depending on fuel load), it can resist a LOT of side load. So far, so good, this is a very stable car, which gets my vote. However, the gyroscopic effects can also be very powerful.
The Car has 4 x 95 kg aluminium wheels. At the Car’s peak speed of 1000 mph, the wheels will be rotating at just over 10,000 rpm. The question is, will these 4 huge high-speed ‘gyroscopes’ be able to generate enough precession force to roll the Car over?
In order for gyroscopic precession to roll the Car over, it would have to generate a rolling moment equivalent to a side load of 7-8 tonnes. Doing some very rough gyroscope sums (if you want an exact answer, you can do your own vector maths at home!), creating that much gyroscopic precession would require a yaw rate of over 500 degrees per second. That’s a huge yaw rate. Fortunately, we are never going to get anywhere close to it, as we can rely on the world’s hardest-working aerodynamic fin to keep the Car straight (talking of which, have you put your name on BLOODHOUND’s Fin yet? And if you have, then why not put a Selfie on the Car as well?).
Stability and drag
Of course, nothing comes for free. Most of this stability comes from the widely spaced rear wheels, which stick out into the supersonic airflow. As a result, the rear wheels/suspension generate nearly half the aerodynamic drag of the vehicle, so the jet and rocket engines have to work very hard to overcome this enormous drag force. I may be slightly biased (OK, I am very biased in this respect) but this extra drag is a small price to pay for safety.
So much for the gyroscopic effect on the whole Car. What about the effect on the front wheels, while I’m steering? The gyroscopic precession will be minimal, as I won’t be turning the wheels that quickly. In fact, I probably won’t be able to turn the wheels quickly, even if I wanted to. The gyroscopic rigidity may well make the steering extremely stiff at high speeds, so rapid steering inputs will be very difficult. Once again, the Fin should do most of the work in keeping the Car straight at supersonic speeds.
The steering will also be affected by the Car’s movement on its suspension, and this is more complicated. Over a year ago, we laser scanned the Hakskeen Pan track in South Africa. The surface is basically very smooth, but it’s not perfect. We know that the Car will experience tiny rolling movements, due to the surface variation, steering inputs, small gusts of crosswind, and so on.
To cope with these tiny rolling movements, we’ve designed the suspension geometry to minimise the roll effect on the wheels, so there’s minimal gyroscopic precession. However, as mentioned previously, nothing comes for free. Setting the suspension up to keep the wheels vertical during body roll will mean that if an individual wheel hits a small bump or dip, it will move up (or down) and lean over slightly. This will put a gyroscopic precession force through the steering wheel. As a result, I may feel the steering wheel twitching from side to side in my hands, at very high speed.
Alternatively, the very sudden precession force (added to the original bump load on the affected wheel) may just cause the suspension bearings to stiffen up under load, making it more difficult to steer the Car smoothly at high speed. I’ll find out when we get there – and thanks to the live video and data streaming from the Car, you’ll find out at the same time as I do!
Gently does it
While I’ve been worrying about how to steer the Car in a straight line, the BLOODHOUND Education Team has been delivering a huge success with the launch of the BBC micro:bit model rocket car competition. Aulden and his small dedicated team have worked incredibly hard to launch this national competition, through 120 BLOODHOUND hubs across the UK. The results they’ve delivered are simply staggering. With 10,000 school teams taking part over the next 2 months, this is the largest STEM education competition in history.
The micro:bit technology will be used for every competition including the regional heats, leading up to the national finals at Santa Pod Raceway at the end of June. Every run will have electronic timing, as well as micro:bit sensors carried on the model rocket cars to record every rocket-powered run. Gone are the days when young students have to guess at the performance and how to improve next time. Now they can download the data, analyse exactly what happened, and engineer their improvements based on the data. This is another example of the ‘BLOODHOUND Effect’, inspiring young people to engage in science and technology in the most exciting way possible. Good luck to all 10,000 teams, we’ll look forward to seeing the winners at Newquay next year as our guests at the live runway testing of BLOODHOUND SSC!