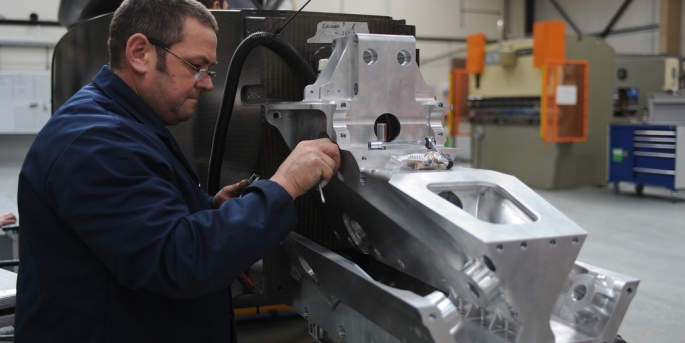
The front suspension sub-assembly
Otherwise known as the ‘goats head’. This is made up of four huge five-axis machinings that are made from 7075 forgings (7075 being the specific alloy and forged parts being used for greatest strength and therefore control of residual stresses). We spent many weeks searching for these and in the end thyssenkrupp Materials came up trumps, finding what we needed in just the right size! This was great news as a bespoke mill run for this material could easily have added six months to the project. The team at the AMRC in Sheffield have machined these parts on two new CNC machines and done a simply stunning job.
When we say “huge”, we really mean it. The upper parts had a start weight of 313kg each but finished up weighing just 18kg each – that’s 94% of the metal removed. The lower two parts started at 149kg each and had 89% of the metal removed, ending up at 16kg each. Add all this together and the total start weight for the whole assembly was 924kg – yet the four parts of the assembly together now weigh just 68kg.
How long did it take to remove all that material? The billets were on the machine for 103 days, with the spindle turning and cutting for 97 of those. Overall it took 151 man days from operators, project engineering and project management to deliver these stunning parts.
Both the material and the machining for this task have been fully sponsored. This is amazing when you consider that for the price of the materials, project management, programming, machining and inspection you could easily fill a not insignificant garage full of your favourite super cars. It’s also amazing when you remember that this is just one key assembly of BLOODHOUND SSC and that this cost does not include the great work by our design team, which conceived the part in the first place, or our great assembly team that has to put it all together!
The goat’s head was a major challenge but a further 268 parts are needed to complete the entire front suspension sub assembly. Many of these are already made and the balance soon will be designed and manufactured.
- by Conor La Grue
Check out Delcam's video of how thier software was used in the manufacturing process: