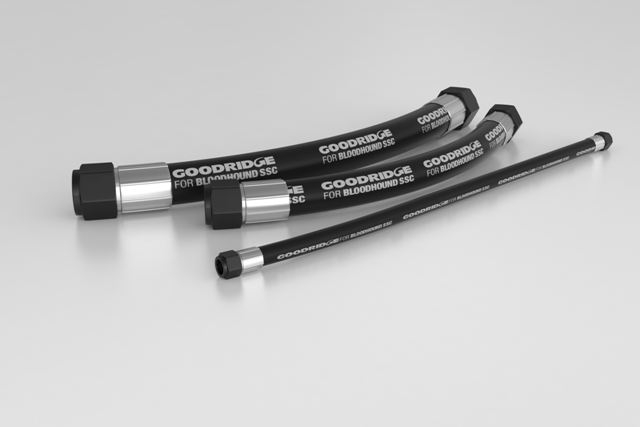
Given the critical role of performance fluid transfer systems in Bloodhound SSC’s success and safety, it seems only natural that the world’s leading manufacturer should be entrusted with supplying them.
All of the vehicle’s fuel, cooling, braking and air conditioning hoses, pipes and fittings are manufactured and supplied by Goodridge. But the relationship doesn’t end there, as Goodridge is also a stripe (financial) as well as product sponsor.
Close involvement in land speed records is nothing new to the global company – headquartered in Exeter. In fact, the relationship with Richard Noble’s record-breaking cars extends back as far as Thrust 2 – which broke the record in October 1983 – and includes contributing to the successful Thrust SSC project in which Andy Green famously smashed the sound barrier 14 years later.
Founder Stuart Goodridge always had a love of speed, starting from when he gained his private pilot’s licence when only 17 at his native Southport, Lancashire. Moving to Canada, he raced single seat and sports cars with significant success, forming his own team with two friends. While still racing, Goodridge started making his own high performance brake lines, eventually supplying these and racing parts to other teams. At 23 he returned to the UK, borrowed £50 from his brother to buy an off-the shelf company and started making brake lines on his mother’s kitchen table. The rest, as they say, is history.
Today, the business is still privately owned and has a turnover of £30 million. It manufactures in ten strategically located facilities around the world and has a workforce of 300, of whom over 100 are in the UK. It’s a process that uses state-of-the-art technology throughout, as the video on the company’s home page demonstrates. Goodridge is a very well known name in motorsport circles, yet this is actually its smallest market – others include OEM (original equipment manufacture) and motorcycle and car retail aftermarket kits. Sadly, Stuart Goodridge passed away in January 2011, at which point his widow Trudi became a non-executive director, having worked in the business for many years.
When Stuart Goodridge learned of Richard Noble’s latest land speed record attempt and his desire to smash the 1,000 mph barrier, he naturally wished to get involved again. He consulted fellow directors Bill Ray (Group MD) and Jon Hanna, who had both joined the board in 2008.
Hanna told us “We all agreed that the company should support Bloodhound. We were fired up by the idea that it’s designed and built in the UK, at the very cutting edge of technology and also by the very strong educational aspects of the project. We were keen that our products be central to its success.”
A close working relationship between Goodridge and the Bloodhound SSC team ensures that technical and logistical requirements are always met. Goodridge is highly reactive in that Bloodhound’s engineers state the requirement, and Goodridge supplies the best hose, tube or fittings to suit. There’s also a consultative aspect to the relationship in that Goodridge’s engineers often suggest an alternative, more effective means of achieving the desired result.
Many of the hoses supplied are of the company’s motor racing and aviation-grade type which is covered with a firesleeve. The steel braiding ensures the requisite strength and that no swelling or contraction occurs, whilst PTFE inner cores ensure zero contamination. Other hoses are automotive OEM or aftermarket types supplied off the shelf – testament to the quality and reliability of Goodridge’s standard offering.
According to Jon Hanna, one of Goodridge’s toughest challenges to date has been to accommodate a combination of extreme temperature, vibration and tight routing. “The volume and speed of the HTP oxidiser pumped from the tank to the rocket would fill a bath in seconds,” he explains. “We’ve had to introduce a large diameter hose with very tight bend radii in order to accommodate the routing, and in order to achieve this we’ve had to consult with our suppliers to ensure the most appropriate product.” He continues “Much of what we’re doing on this project has not been done before, so we’re having to innovate as we go along, engineering solutions in close cooperation with the project’s designers.”
The relationship between Goodridge and the Bloodhound SSC team is principally with the company’s Exeter HQ, although a substantial amount of product is supplied via its Silverstone facility owing to its proximity to Cosworth.