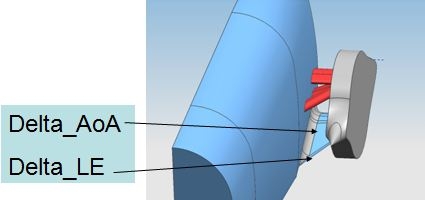
In the last article, we looked at the Parametric Study done by the Engineering Design team. The whole purpose of this was to determine which factors strongly influenced the lift and drag at the rear of the car and which to take forward to the next step, the "Design of Experiments" or "DoE" for short. Of the 18 factors investigated, 6 geometric parameters stood out as being crucial to the character of the car at high Mach numbers. Of those, one was so powerful that it was decided to fix it, and not vary it at all during the DoE.
So, what is a Design of Experiments? It’s best described as a way to predict the best solution to a problem from the results of several “experiments”, even though you may never chance upon the “best” solution during your experiments. In our case the “experiment” is the result of the CFD analysis from varying the five parameters detailed below, without trying every possible combination at every possible value. A more detailed explanation of how we’ve applied DoE to this, and other aspects of the design of BLOODHOUND SSC, will be published in a future part of this series.
Key to this was the ability to rapidly create the design changes, mesh them and get them through the CFD analysis. We used the NX model developed for the parametric study and refined it to be directly driven from a list of the five variable combinations. This is a simplified model and lacks some of the finesse you may be used to seeing – things like the wheel fairings are quite “blocky” (and in fact don’t contain rotating wheels) but the importance for us was the speed that the model could be generated, and, as importantly that it could be reliably and repeatably meshed for analysis.
Five design features of BLOODHOUND SSC were studied in a lot more detail. These were the major contributors to drag and lift that were discovered in the parametric study. What effect did varying these have on the drag and the lift? What is the optimal value which would lead to the best design for the car? Time to put the Swansea aerodynamicists and the Intel processors to work again!
The five features were:
- delta leading edge sweep angle
- base area
- boat-tail angle
- delta angle of attack
- 'spam' shape
Delta AoA and Delta LE
The delta is 'filled in' part of the lower rear suspension; the idea of this being to prevent the supersonic shock waves from going underneath the car and causing the lift. Looking at the car from above, these form a triangle ... hence the name 'delta'.
Two variables were studied - the Angle of Attack ('AoA' in the diagram below) is the angle between the car body and the delta. Leading Edge ('LE' below) is the point along the body where the delta joins.
Spam
Spam is the name given to the cross-sectional shape of the car; should the sides be vertical or angled in towards the top? The name was first used to describe a curvy variant of Config 2 – “Spamhound” - and actually derives from the traditional shape of a tin of ham!
Rump
The rump is the point where the back of the car starts to narrow. Should this be forward of the rear wheels, or more toward the back?
Cone
The cone refers to the shape of the back of the car - how much should it hug the lines of the jet and rocket engines? Imagine half a cone taken away from each side - how big should this be?
In order to give a good result, 43 slightly different models were needed to allow us to predict the best solution for a combination of all five variables. To put this workload into perspective, in the 18 months to November ’09 we had modelled, meshed and analysed around 14 configurations, in 3 weeks in January we modelled, meshed and analysed all 43 models of the DoE.
Wheel Track
The one we fixed, the most powerful factor of all, that was the rear wheel track, and has sparked quite an internal debate on just how to create a stable supersonic car. (see Brian Lecomber's ghost of run56).
The final part in the Design of Experiments saga, the clever bit, is how you take all this analysis data and pluck out the winning solution. We are lucky enough to have MathWorks on board, and their help has been crucial in making the best use of the tools available within the MatLab suite of software. The next article, to be published in early April, will go over the results, and show how after 22 months of trying, we are finally coming to fully understand the aerodynamics of a 1000mph car.