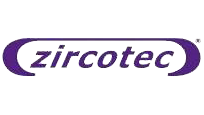
Cooling a 135,000bhp, 1000mph car poses critical challenges for safety and performance that now, just months ahead of the first run, the BLOODHOUND team is looking to solve
As the build of BLOODHOUND SSC gains momentum and a planned UK test in Newquay is just months away, engineers are increasingly looking at the detail design challenges to help them push the car to 1000mph and above. These include the issues of cooling the tightly-packaged Rocket engine together with ensuring the volatile HTP (High Test Peroxide) doesn’t decompose before it reaches the rocket chamber and in effect, become a bomb.
“We’ve got approximately 1000 litres of HTP that has the equivalent explosive force of 1 stick of dynamite per litre if it reaches 40°C, and starts to decompose” says Tony Parraman, of the sponsorship liaison team. “Packaging dictates that our supercharged Jaguar engine, that we use to pump 900 litres in just 20 seconds, is sat next to the tank so preventing heat transfer is on our essential list.”
As a prime source of heat in proximity to the tank, the BLOODHOUND SSC team specified Zircotec’s ThermoHold® ceramic coating for the Jaguar exhaust. Plasma-sprayed at twice the speed of sound itself, the coating can reduce surface temperatures by at least 30 percent, ensuring even as heat builds up during the two runs needed for the record to be validated, the tank remains stable.
Unlike previous record challenging cars, a large proportion of the BLOODHOUND front structure is composite. Chosen for its excellent strength/weight ratio, the drawback of composites is its poor resistance to temperature compared to metallic options. “We turned to Zircotec again,” adds Parraman. “We know that they have supplied heat resistant coatings to F1 teams for years, literally preventing the delamination of carbon fibre in high temperature environments, enabling the material to be used above its traditional melting point.” Zircotec proposed ThermoHold® for Composites, a zirconia-based coating that is applied at temperatures exceeding 10,000°C but in such a way that the substrate is unaffected. “Zircotec’s patented technology for protecting composites offers a huge benefit, allowing the use of lightweight materials in places where they are exposed to significant heat. Our engineers are not experts in thermal management and having Zircotec’s technical support is helping to ensure we only use the coating where it is needed, saving weight where we can,” adds Parraman. “We have used the coating on the composite upper chassis hoop, offering lightweight resistance that lowers surface temperatures by 100°C.”
Digging deeper into the Zircotec parts bin has seen BLOODHOUND pick ZircoFlex®. The proven hybrid aluminium/ceramic heatshield, just 0.3mm thick, is being applied around any areas of the vehicle where heat is expected and needs to be resisted. “With ZircoFlex® we can bend and mould it to shape, it’s lightweight and with self-adhesive backing, good for up to 500°C, we can use in lots of areas,” claims Parraman. “For example after a two minute run, the internal temp of the jet or rocket might be 3000°C but the externals are 200°C. We can manage that heat with ZircoFlex®, protecting wiring looms and composite panels.”
With ambient temperatures of 40°C expected in the South African desert, Zircotec is being relied upon to keep temperatures down during the critical time slot of one hour between the two runs. “We’ve got 60 minutes to turn the car ‘around,” adds Parraman. “We want to prevent heat soak during this time. It will help us work faster without the risk of getting burnt and if we need to change the rocket, it should speed up changeover time.”
The team will trial the car in South Africa, providing a real test of the thermal protection. “We plan to thermocouple the car and see where the heat issues are,” suggests Parraman. “It’s a one-off and we are pushing the boundaries so we don’t know all the answers. Once we do, we’ll be working with Zircotec to ensure that when we do get to Hakseen Pan in South Africa we are fully prepared to deal with the heat.”
Cooling a 135,000bhp, 1000mph car poses critical challenges for safety and performance for the BLOODHOUND team used the coating on the composite upper chassis hoop, offering lightweight resistance that lowers surface temperatures by 100°C.
Zircotec’s Plasma Spray process applies material at twice the speed of sound using a torch running at over 10,000°C
About Zircotec
Zircotec www.zircotec.com offers a wide range of plasma-sprayed ceramic and metallic coatings that protect components against the effects of heat, wear, abrasion and corrosion. Lightweight and easily packaged, Zircotec’s technologies can be applied to a broad range of different materials including metals and composites. Proven in F1 and the nuclear industry, the technology is now trusted by car manufacturers, industrial users, car enthusiasts and an increasing range of other applications to effectively manage heat and wear, enhancing performance and reliability. ZircoFlex® offers for the first time, a truly flexible ceramic heat shield material.
Press Enquiries
Zircotec
Nick Bailey, Elan PR Ltd +44 (0) 7813 956664
nick@elan-pr.com
Sales Enquiries
Zircotec
Peter Whyman, Zircotec, 22 Nuffield Way, Abingdon, Oxon, OX14 1RL
+44 1235 54 60 50
peter.whyman@zircotec.com