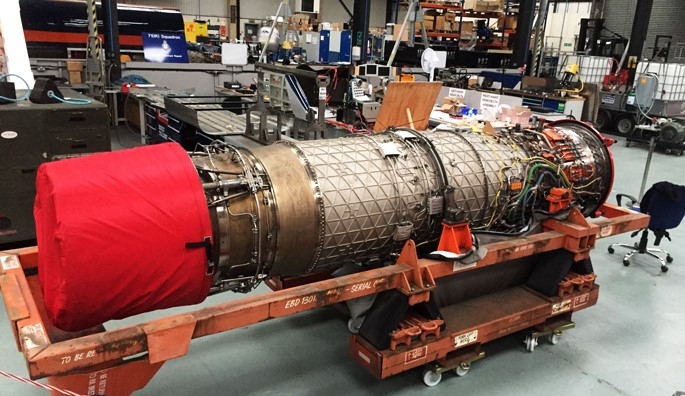
As the Team prepares BLOODHOUND SSC for the runs at Newquay in October, it’s all go at the Technical Centre (BTC). Parts continue to arrive from suppliers and before long we should have all bespoke BLOODHOUND-designed parts necessary to build the Newquay-specific car configuration.
So the Car is really coming together, but there's a great deal still to do before the first turn of the jet engine. Things are definitely hotting up. Here’s some of the work that’s happened at the BTC in the last month….
Anchor points and seat
Carbon composite specialist Dave Haggas has been fitting the anchor points on the monocoque, starting with those for the heat shields and floor braces and moving onto Andy's seat and head restraint mounting points. This involved dry fitting and glue-squeezing the seat into the cockpit ready to install hard points into the monocoque structure, skilfully overcoming some of the challenges with carbon composites caused by variations in manufacturing tolerances.
Thanks to the skilful hand of Dave Haggas, the seat can now be easily installed and removed to precisely the same position each time. This includes the dog bones, which are used to secure the top of Andy’s six-point harness and acts as a key reference point for the location of the seat as a whole.
The jet engine
The Systems team has run off-car testing of the jet control system, and calibrated the strain gauges on the suspension pull rods and the EJ200 thrust links so that the suspension and thrust loads can be captured and analysed every time the Car runs.
One very exciting event this month was the arrival of the operational EJ200 jet engine that will be fitted to the Car, paving the way for hardware-in-the-loop (HWIL) engine control testing.
Separately, as the auxiliary jet fuel tanks won't be used during the trials, one is being blanked off and the other removed while the rails and trellises were removed to fit panel brackets.
Suspension
The front suspension is now mechanically fully assembled and installing the all-important brake lines has begun. In preparation for the rear suspension, the structural tubes have been subjected to dye-pen inspection, which is a non-destructive testing (NDT) method to identify and cracks or voids in the welds. As these parts are key to distributing loads through the back end of the Car, it’s important their structural integrity is satisfactory.
The blade
The carbon blade structure manufactured by URT has been weighed, and strain gauge datums recorded and fastened to the monocoque. We needed to ensure the blade was nicely balanced as it was lifted and manipulated through the front suspension; and it located with ease onto the mounting points.
Nearly there…
So the Car now really looks like it is coming back together, with much of the off-Car systems testing completing for the Newquay jet car configuration. With more systems and sensors going on the car, and the accompanying looms, we will be dealing with niggles and custom fits for a few more weeks, however. Why, you may ask? We’ll it’s not always time-efficient to model absolutely everything in CAD. For a prototype vehicle, some parts are best left to skilful tailoring in-situ.