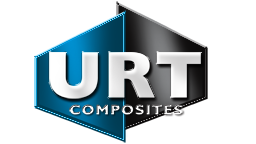
There has been lots of fantastic work done at Bloodhound SSC Sponsor URT Group Ltd over the last few months. If you look on their website, they proudly say "URT Group is a high-quality manufacturer of composite parts and structures".
Bloodhound SSC's Engineering Lead (Commercial) Conor La Grue and Stuart Allen, Bloodhound SSC's Composite Lead have been watching progress of the monocoque build and would certainly agree!
The story starts back in July 2012 when the patterns for the moulds were machined out of two tonnes of tooling block- see Conor's blog "Chassis Progress" and the picture right.
Two moulds were made, one for the lower section and one for the upper section. The upper section can be seen above, and a view inside lower section is right where the next stage has been started - putting in pins and markers where the holes need to be.
A "splash" was made from each mould - a quick first make of the sections - and delivered to the Bloodhound Technical Centre in Bristol. The splashes were used to mock up driver Andy Green's cockpit to give an early realistic impression of the space inside the cockpit to determine where all the instruments and controls go.
In the picture left, British Army Metalsmith Graham Sargeant tries the instrument panel position with Andy as Conor La Grue and James Painter look on.
URT then set about manufacturing the real monocoque, and Andy visited them in early January 2013. Andy not only wanted to see the progress being made, but also help out and learn more about the process for himself. (below left and right)
Andy went some way to repaying the staff at URT by giving them a talk about the project. (below)
Andy's visit was shown on the local BBC news:
The team at URT continued to add more layers of carbon fibre, making sure that the structure was strong where it needed to be
Once all the layers on carbon fibre had been added to the moulds, the two halves were then brought together - picture left below shows the last few layers on the join from inside - and vacuum-packed and baked in an autoclave.(picture below right).
Several hours later, the monocoque was unwrapped. Conor's comment - "fantastic job, really stunning work!"