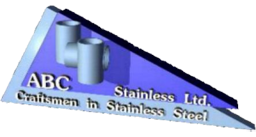
The ground breaking way in which the Bloodhound SSC team is designing the vehicle to quite literally rocket it to over 1000mph, has meant overcoming substantial engineering and design challenges in all areas of its development. This is the case for not only the development team itself, but also for companies supplying products, technology and expertise to the project.
The challenge for Peterborough-based ABC Stainless Ltd was to design and build the tank holding 1000 litres – one tonne – of HTP (High Test Peroxide) liquid oxidiser before it is pumped in just 17 seconds into the vehicle’s Falcon hybrid rocket at its UK test firings. Storage and handling of HTP requires special care and equipment, as it is incompatible with many common substances including iron and copper, which catalyse its exothermic decomposition into steam, oxygen and intense heat.
ABC Stainless Directors Mark McAuliffe (left) and Justin Woolner – both self-confessed ‘petrolheads’ – agreed to lend their expertise in stainless steel design and fabrication after Justin had met Richard Noble and Andy Green at the 2009 Goodwood Festival of Speed and joined the 1K Club. After a visit to their Peterborough factory by Bloodhound Engineering Lead Conor La Grue to talk through what they could offer, they were briefed by Senior Control Systems Engineer Dr John Davis on the exact requirements for the tank.
It was originally thought that the same tank may be used for test firings and in the vehicle itself. This is now probably not the case, but it does go part of the way to explaining why it was designed with its unusual shape. The other reason is that although the HTP will not be under massive pressure, the perfect shape for a pressure vessel is a sphere, and the final version is as close as possible to this whilst still achieving the required capacity. Strength is further enhanced by a series of internal ribs and baffles, which also minimise movement of the tank’s contents.
Right One of the HTP tank design documents
The tank’s design, produced by ABC Stainless, was evolved and refined over time in close consultation with John Davis, and also Bloodhound’s James Painter and Stress Engineer Roland Dennison using Finite Element Analysis software. For example, computer modelling of an early version indicated potential deflection under pressure, so the ends were rounded more accordingly.
The tank’s ends were formed by rotating and rolling sheet stainless steel into hemispheres which were then cut in half and TIG butt-welded with another section to form ovals, which were in turn welded to the main section. The flanges, pipes and connectors were then attached before the entire assembly was bead-blasted.
To minimise the possibility of contamination of the HTP, the internals of the tank had to undergo a ‘pickling and passivation’ process carried out by Birmingham-based firm Anapol.
Left: The stresses on the tank needed to be analysed
The tank was immersed in a hydrofluoric acid solution which micro-etches away the surface layer of oxide, then passivated to restore its stainless qualities by immersion in a nitric acid solution, prior to being tested by the Bloodhound team by filling it with HTP.
ABC Stainless has also supplied other, smaller components to the project – namely the tank and pipework to supply warm water to preheat the Cosworth F1 engine which drives the HTP pump before it is started, and the ice tank to supply the water that cools it down.
Mark McAuliffe told us: “It’s been a fascinating process. We have a passion for speed and enjoy a good challenge which involves overcoming problems by finding the most appropriate answers.”
Right:The HTP tank being maunfactured
ABC Stainless claims to be the best-equipped stainless steel fabrication company in East Anglia, with laser jet cutting, water jet cutting to a thickness of 10cm and a dedicated workforce of 30, most of whom have been with the company for many years. Its main markets are oil/gas/petrochemicals, pharmaceuticals, food and drink and architectural features. It counts many well known names amongst its customers, including Rolls-Royce.
Below: ABC have also manufactured the cooling tank