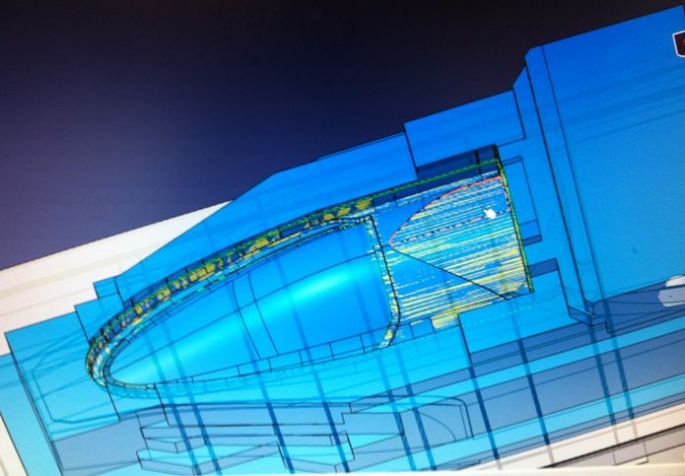
I’m late with my blog this month, sorry! Being on the road increasingly as the build progresses creates time that’s hard to make productive! The face to face meetings are really great, but then the time in the car can be hugely frustrating. Yes I can catch up on phone calls, but you can’t make notes or reference documents during the call and that very likely leads to a follow up call or email once I’m back in the office.
A really busy last couple of weeks in May left me with a significant backlog of tasks and emails one of which was a reminder to complete my blog!
I’ve been lucky enough to work in Engineering and Operations disciplines in multiple industries: Defence, Oil Industry (up stream exploration equipment), Emerging telephony and motorsport. As we all do, I have picked up management practices along the way that have worked for me to help me get things done. One of those is a simple traffic light scheme on outstanding tasks and no matter what the industry or project, completed honestly it gives you a very raw view of where you really are with progress. Red, amber and green it starts off a painful and shocking page of reds, which slowly migrates to amber and the lines of green only dawn as you start to get the job done!
Throughout May and early June the lower chassis components that have been completed by the good works of BHW Wigan Hampson and Amada, with materials supplied by thyssenkrupp Materials, has led to the lower chassis task list going almost completely green. With all the remaining components programming completed by Jaivel and material in hand, we’re looking really good on the rear lower chassis build.
I like green!, it’s one of my favourite colours and for weeks now I’ve found myself getting the Bill of materials for the rear chassis out of my bag and showing people - “Here look, see this sheet here, this is the rear chassis lower section – and green means the part is completed!” So green, for good reason makes me smile! The conversation around the rear lower chassis has now very much shifted to the rivets, bonding scheme and painting / plating of the lower chassis components. It’s a very exciting time as the first major chassis assembly comes together!
As the first large section for the rear get close to being a completed, the carbon composite front of the car has also come on leaps and bounds since last I wrote. The Monocoque aka “Andy’s office” – has started to also transition from the CAD environment, to the real world. After sterling work by all the design team, especially our Lead Composites Engineer Stuart Allen, the detailed design data has been flowing at pace into UMECO.
Last week UMECO began to cut the male pattern for the composite tool, with over a tonne of tooling block for this “smaller” lower section and the blocking up of the upper to follow close behind this monster male pattern will be being machined night and day for over a week. The male pattern will then be hand finished and the lay up of the female composite mould will begin.
We plan to produce both the upper and lower female composite moulds and then bolt them together top and bottom to check the alignment before we lay up the actual parts. The law of sod comes into play here - there is a lot more material in the upper mould so expansion may mean it grows a little and so we may need to fettle the moulds to make sure we have a part that matches the surface model.
This means the lay up of the Monocoque upper and lower section will now happen in parallel and this major chunk of car will very quickly become a reality. I’ve been working with the fantastic team at UMECO for over three years to get to this point and it’s incredibly exciting to pay a visit and see this huge pattern being machined. 100 days of red, turning amber and then dawning green will see this huge composite assembly take shape, simply fantastic and so exciting for the everyone involved with the Project.