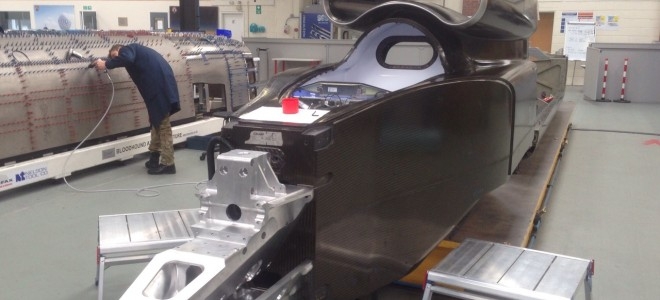
Let me tell you about the goat’s head that’s worth more than a garage full of your favourite supercars….
This particular ‘goat’s head’ is actually the hardest working, land-based vehicle suspension component in human history!
As a team we have a good or bad habit (depending on your viewpoint) of giving key assemblies for Bloodhound SSC nicknames.
The 'Bloodhound 'goat's head'
In this case, when the topological optimisation study was done on the front suspension, what the computers spat out looked spookily like a goat’s skull and the name has stuck ever since.
And in case you’re wondering how this ‘topological optimisation’ works, in our very clever stress analysis computer, we start with a big, plain block of ‘virtual material’, put the mounting points in and let the computer ‘eat away’ any material that isn’t dealing with the actual loads. That results in the ideal form for the part.
Front suspension
April came and went and here we are in May with several milestones under our belts; milestones that are critical to us delivering a complete car next summer to Hakskeen Pan.
The first of these milestones is the aforementioned goat’s head – otherwise known as the ‘front suspension sub assembly’.
This is made up of four huge five-axis machinings that are made from 7075 forgings (7075 being the specific alloy and forged parts being used for greatest strength and therefore control of residual stresses).
We spent many weeks searching for these and in the end thyssenkrupp Materials came up trumps, finding what we needed in just the right size! This was great news as a bespoke mill run for this material could easily have added six months to the project. The team at the AMRC in Sheffield have machined these parts on two new CNC machines and done a simply stunning job.
When we say “huge”, we really mean it. The upper parts had a start weight of 313kg each but finished up weighing just 18kg each – that’s 94% of the metal removed.
The lower two parts started at 149kg each and had 89% of the metal removed, ending up at 16kg each. Add all this together and the total start weight for the whole assembly was 924kg – yet the four parts of the assembly together now weigh just 68kg.
How long did it take to remove all that material?
The billets were on the machine for 103 days, with the spindle turning and cutting for 97 of those. Overall it took 151 man days from operators, project engineering and project management to deliver these stunning parts.
Both the material and the machining for this task have been fully sponsored. This is amazing when you consider that for the price of the materials, project management, programming, machining and inspection you could easily fill a not insignificant garage full of your favourite super cars. It’s also amazing when you remember that this is just one key assembly of Bloodhound SSC and that this cost does not include the great work by our design team, which conceived the part in the first place, or our great assembly team that has to put it all together!
The goat’s head was a major challenge but a further 268 parts are needed to complete the entire front suspension sub assembly. Many of these are already made and the balance soon will be designed and manufactured.
First desert wheel
Spin tests took place on the Bloodhound car’s specially designed wheels at Rolls-Royce in Derby
The second major milestone that we passed recently was the physical fulfilment of a four year development programme when our desert spin test wheel arrived. It wasn’t with us for long, as it was shipped back out the very same day for spin tests at Rolls Royce Derby, but it was a vital step to getting the car operational. When this test is a success we can release the final design and machine the remaining wheels to make up both a full car set and a spare set.
We plan to keep back four uncut wheel forgings so that we can tweak the design after the first year’s desert runs. This will allow us to have the ultimate set optimised and manufactured ready for the second season for our fastest runs – and ultimately to help us reach our 1000mph target.
We’ve had an amazing syndicate of companies helping us to get to this stage with the wheels, to whom we are very grateful.
Final area of primary car structure starts to release
Our third milestone has been the completion of the design of some of the remaining front structure composites. We have now started to release the pattern work for some of these very large remaining parts from which we make the composite moulds from which we make the final composite parts.
Our three man composite team, overseen by Brian Coombs, have done a fantastic job of getting to grips with designing these remaining components and getting to the stage where these can start to be released to URT for manufacture.
The release of front end composites is an important stage for us because it’s the last area that we didn’t have a design scheme for and the last area to go into final detailed design. Not surprisingly that also means these are going to be some of the last parts we make and bolt together to ensure delivery of the car next summer.
The composite team have a huge amount of work to get through but the good news is the pattern work is starting to move and and the team are doing a great job of getting through their part of this process.
Get involved!
These are just three of the activities we have been working on this spring – albeit vital ones – but elsewhere we are also maintaining the momentum that carried us so positively into 2014 and we are all working flat out to keep the build on track.
With so much happening daily on the project now why not join our supporters’ club – the 1K Club – so you can see the progress for yourself at the club events? You can also follow our progress on the website, Facebook and Twitter!