Extreme machines need extreme teams
It’s the middle of February 2015 and I realise I’m guilty of not stopping to write my blog for a while! In my defence it’s been an extraordinary few months: our very high work rate has ratcheted up even further, in a way none of us could foresee.
Not only does a BLOODHOUND day start very early indeed, but the 110+ hour, 7 day working week is simply what it’s going to take to get the car operational this year.
Production challenges
To give you an idea how busy it is at the BLOODHOUND Technical Centre, we released as many parts into manufacture in the last 9 weeks as we did in the whole of 2013. In addition, we are currently completing and fitting some very large structural parts.
The challenges presented by some of these parts are huge and, at this stage, if just one major component needs to be remade it could potentially cause the project to slip out of the dry running season! So as each part is successfully completed, I sleep just a little better.
Pump, blades and more
Unlike many organisations we didn’t close shop over the Christmas holiday. That extra effort bore fruit last week when the team was able to conduct some water pump tests with our new HTP pump.

We are part way through integrating the Jaguar supercharged V8 engine into the car as the power plant that will run the rocket pump. This is going really well, which is a huge boost for everyone who has worked long hours to make sure it happens on time.

In the last few days the composite blade upper and lower sections – the very heart of the front of the car – have arrived. They look stunning! These parts have been difficult to design and manufacture, and it’s thanks to great work by our design team and our partnerships with
URT,
SHD Composites and
Sigmatex that these parts have been delivered within an extraordinarily tight timescale.
Now, as we head into the last few months of the car design, the parts are getting smaller but no less complex and the lead times are ever more aggressive. Every part we design and order is something that is being made for the first time ever and the challenge to our supply chain is still increasing – we have to hit our lead times (and ideally beat them) to ensure the car will be operational this season.
Surface table and support kit
In other news, we have added another large surface table to allow us to build up the front of the car while continuing work on the rear. This means that in days, not weeks, we will see what the full length of the car looks like for the first time! For those of us who have worked on the BLOODHOUND Project since the beginning (and I include our brilliant team of suppliers and partners here, as well as the onsite BLOODHOUND team), this is the culmination of years of work – it makes all of us incredibly proud to see what we have produced between us.
We’re also spending more time on designing and building “the stuff to build the stuff”. This is the support kit; initially focusing on assembly-based tooling so we can put the car together, after which we will start to spend more time on the kit needed to operate the car successfully this year on Hakskeenpan.
Success in South Africa
Our partnerships in South Africa are evolving all the time, with critical resources and systems are being driven into place. Martyn Davidson, our Operations Director, and his team are working hard to make sure that when we finish building the car we also have all of our dominos lined up to deploy and run the car safely and effectively in what is an incredibly remote location.
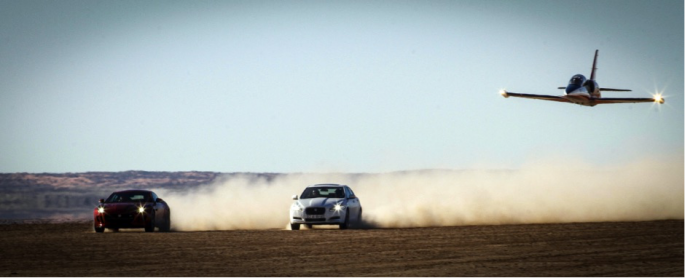
Heading towards the finishing line
In around 8 weeks’ time all the parts that we still have to draw will be completed and released, and then it will be a last dash to the finishing line to complete them on time and on budget – and give our eager assembly team everything they need to finish building the car. It’s a real team effort at BLOODHOUND now, and with such long hours and such a huge amount of effort going into the Project, we feel that we definitely can complete the car in time to run it during 2015.
In all of this, what helps to motivate us is that the BLOODHOUND Project is not just about building a 1,000mph car. It’s about inspiring a generation of girls and boys to discover, enjoy and pursue science, technology engineering and maths. So just as the car starts to look more like a car, the education programme is also going from strength to strength. The adventure is just beginning….
Blog by Conor La Gruecon