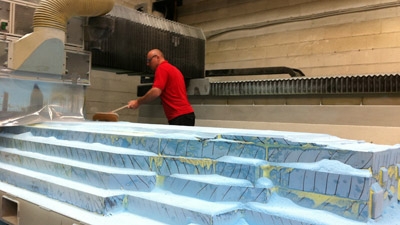
Just a few weeks back I found myself on the BLOODHOUND stand at this year’s Goodwood Festival of Speed. Stella and all the events team had done an amazing job and the stand, I have to say was one of the best that we have ever had. There were multiple "Build Info Zones" with videos telling the story of various components that are in manufacture. This was a fantastic resource for when visitors asked how the build was going and also a great way to promote our partners involvement at the show. Thanks to Oliver at Bellstone.co.uk for an amazing job on the stand displays yet again!
Helping to set up the last few bits on the stand that morning, I was lucky enough to add the thyssenkrupp Materials logo to the show car myself. Their support has been vital for the rear chassis build. Stepping back and looking at their logo on the car, it looked really good and it feels great to recognise and promote what’s been a vital partnership to maintain progress on the rear chassis.
The rear chassis design and build is moving at a very fast pace now. The structure is a mixture of Steels, aerospace grade Aluminium and Titanium alloys, and as I type, the last few parts of the lower section are in WIP at HAMPSON and AMADA, and we are about to start releasing the upper chassis components into manufacture. TWI have done a great job in validating our bonding method and have completed a huge amount of work in a very short time, so that we have a strategy ready to go for when lower chassis assembly begins at HAMPSON.
I’m currently prepping for a visit to Nuclear AMRC with BLOODHOUND design engineer Mark Elvin to complete a DFM review. The team at Nuclear AMRC will be making the Rear suspension sub frame for us. This is where the thrust from the Rocket is reacted throughout the chassis. Nuclear AMRC are used to making very high precision one offs for use in validation technology for use in a high risk, high integrity environment, a skill set that perfectly suits BLOODHOUND. The facility is truly amazing and will undoubtedly go a long way to developing and maturing the emerging nuclear technologies needed for the UK Nuclear industries future and to develop innovative British techniques and products for export to the wider Nuclear global industry.
This is the top half of the pattern for the carbon composite monocoque being machined out of two tonnes of tooling block. [Pic credit Stefan Marjoram]
Take a look at the pictures above and left taken by Stefan Marjoram (our fantastic in house film maker for Cisco Bloodhound TV) at a recent visit to UMECO. It’s hugely exciting for all involved to see the canopy shape appearing out of the 2 tonnes of tooling block that make up the block up for the upper monocoque section. The team at UMECO are doing fantastic work and delivering to the tight schedule. The monocoque will be the first of multiple assemblies produced in composites by UMECO and as soon as it lands in the work shop early autumn with the build team, the integration task will begin in earnest.
As the summer break and the Olympics approach fast now - it’s a race to get as much done as possible before holidays and factory shut downs kick in! Once everyone is back after the break it will then be a push to get the rest of the primary structure into build and get the car on its wheels!