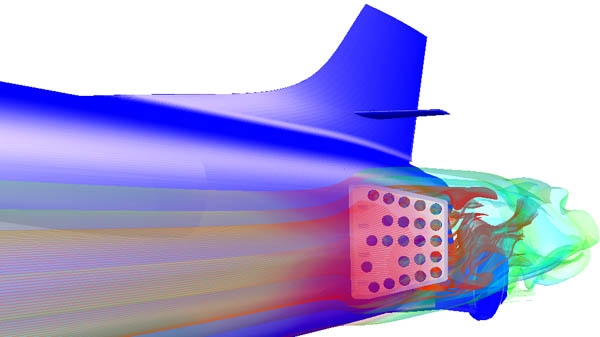
With the virtual Bloodhound SSC car built in 3D CAD, the team used a couple of other bits of clever computer tech to take it for a virtual test drive – right up to 1,000mph.
In the virtual world, there’s no need to create a computer version of Bloodhound pilot Andy Green – instead, it’s a massive supercomputer with the power of an amazing number of smartphones that does the driving.
BloodhoundSSC Engineer
So, what does it do, and why does it need to be so big? Chris Hannon - one of the men who runs these ‘virtual test drives’ - can tell you more.
“When the real car goes up to 1,000mph there will be lots of different forces acting on it.
“The main ones are drag and downforce - caused by the car pushing through the air around it - and stress forces caused by interaction with the ground.
“Our giant computer has two clever tools that work out how these forces affect the ‘virtual’ car before we build it for real - they’re called Computational Fluid Dynamics (CFD) and Finite Element Analysis (FEA).”
In a console game, the processor uses lots of different equations to make your character move within its virtual world but you don’t see them.
It’s the same with testing Bloodhound. The programmes basically work out a whole load of really difficult maths equations – and then tell the engineers what’s happening.
But it’s a lot cooler than just a bunch of numbers. Here’s Chris again to explain more.
“The equations used in CFD can predict how and where every molecule of air is affected by things in their way – including giant rocket cars.
“When the computer crunches the numbers, it’s effectively filling the car’s virtual world with virtual air and then driving it through that air at whatever speed we want.
“Before running the programme, we coat every surface of the virtual car with a mesh – a bit like covering it in wrapping paper with tiny triangles all over it.
“The car has around 20 million triangles on it and once all the sums are done every one of them will turn a different colour depending on the amount of temperature or pressure the equations say is on it.
“Blue and green are good but red means it’s high, which in real life would mean the force or temperature on that part could damage it.
“We can also pick any imaginary air molecule and follow exactly where it goes over time – and that can create moving flow lines which show exactly how the air will move around the car.”
There are literally hundreds of thousands of equations that need to be solved to determine how the air will flow around the car.
Even with the massive computer, the number crunching is so big that engineers have to leave it running for about three days to get the answers.
The engineers use a similar – but less equation intensive, and so less time consuming - process to analyse the stress forces.
The computer is told to apply a load to the car or a specific chosen part of it and the colour of the triangles – now set to display units of stress - show where levels are too high and there is a danger it will fail.
These two techniques are used together in a loop to test, re-design, re-test and re-design – turning it from the initial concept into a detailed virtual prototype ready to be built.
Chris explains: “When Bloodhound was first created, it was drawn in very simple shapes with the most streamlined shape to get it to 1000mph.
“The analysis then showed what parts had to be changed and, over time, the car’s shape was born.”
Now that’s all done. And it’s time to build it for real...