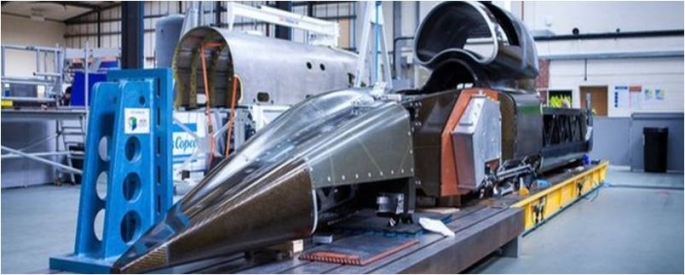
So much to do, so little time. As we race to get BLOODHOUND ready to run this year, we’re still ordering the last of the parts that we need, and putting them together as fast as they arrive. With the usual technical and financial delays (both of which are a standard part of any Land Speed Record attempt), we’re still trying to work out exactly when the Car will be ready for its first runs.
Fitting out the 1000 mph office
Despite the inevitable problems, the whole team is very clear about one thing – short of the end of the world, we will be running BLOODHOUND this year! Have a look at our latest Cisco BHTV video, ‘Building BLOODHOUND in 90 seconds’, to get a (very) quick snapshot of all the work going on right now.
Last week, with the expert advice of specialists from the FIA Institute, we finalised the installation of the seat harness and restraint systems in the cockpit. We’re using off-the-shelf equipment including a standard 6-point race harness, head-and-neck restraint ‘HANS’ device, full-face race helmet, and so on. However, we’ve got to make all this fit around a bespoke carbon-fibre cockpit seat in the unique BLOODHOUND cockpit.
Supersonic air supply
Thanks to the FIA’s advice, we’ve finally got there. The URT seat, Willans harness, Simpson hybrid HANS device and Arai helmet are all fitting together like they were made for each other. Then Camlock turned up with my ‘Adom’ breathing air mask, usually used in the RAF’s Eurofighter Typhoon jets. Uniquely, this will fit under the full-face helmet, giving the best of impact and breathing protection. The mask also fitted perfectly, right down to the length of the air hose. I love it when a plan comes together...
The Royal Air Force technicians are hard at work on BLOODHOUND’s titanium floor and the rear ‘delta’. It’s not strictly speaking a delta: the 2 rear lower suspension fairings, one on either side of the Car, suggest a triangle shape (or ‘delta’) at the back of the Car. This delta shape is a critical part of the Car’s aerodynamics, which must keep the Car safely on the ground all the way up to 1000+ mph. To help us realise that shape, we’ve asked the experts from 71 (Inspection and Repair) Squadron to build it.
Half a ‘delta’
We’re using a lot of titanium under the Car, to protect it from the furious storm of desert dust and grit that will blast BLOODHOUND at supersonic speeds. The problem is that titanium is hard (which is why we’re using it!) and difficult to work – hence we are lucky to have the world-class expertise of the Royal Air Force on the case.
The titanium floor alone has 200 separate pieces (including ribs, stiffeners, stringers, edge members, straps, buttstraps, doublers, brackets and cover plates) held together by 50 bolts and nearly 5000 rivets. Each rivet hole involves pilot drilling, de-burring, pinning, drilling out to full diameter, de-burring again, pinning again, counter sinking and de-burring a final time. You can see why we’ve asked for help with this mammoth task. However, I was slightly concerned to see a picture the other day of one of our most recent ‘assistant technicians’: Adrian Chiles, doing some drilling for Radio 5 Live. I did ask if Adrian had any qualifications to do this. The polite suggestion was not to ask questions I didn’t want to know the answer to....
Have you done this before, Mr Chiles?
Last week all of the aluminium Fin components returned from being anodised. ‘Anodising’ is the process of protecting the aluminium from corrosion. Aluminium naturally protects itself with a very thin layer of oxide, which forms with exposure to air, but chemicals like salt cause the aluminium to corrode despite this. As our desert track in South Africa has a relatively high concentration of salt in the alkali playa surface, we need to protect the Car from corrosion.
Anodising the rear suspension upright
We may only be running the Car for a limited period of time, but we can’t afford it to start rotting away before we’re done. Each aluminium component is submerged in an electrolyte bath and a current is passed through it. The aluminium is the positive electrode or ‘anode’ (hence the term ‘anodising’), which has the effect of making the protective aluminium oxide layer about 1000 times thicker. This anodised layer is still thinner than a human hair, but now protects the surface against corrosion.
When we get BLOODHOUND up to 1000 mph next year, I want to know that the Car is still as good as new, and having everything corrosion-protected is part of making that happen. I’ve just seen the last big parts of the suspension, the rear uprights, being anodised before delivery to the BLOODHOUND Technical Centre. The uprights are the big aluminium bits that carry the wheel and wheel bearings, and bolt directly to the rear suspension arms (including the rear delta mentioned above). It’s going to be a big moment when we finally put BLOODHOUND on its wheels for the first time. I can’t wait.
As well as the Land Speed Record vehicle, we’re busy preparing all the support equipment for record breaking. This includes a towing arm, refuelling equipment for jet and rocket motors, hydraulic and electrical power supplies, air starters for the jet engine – the list goes on. One of the more exciting bits of support equipment is our fleet of Rapid Response Vehicles.
Colourful high speed support
Jaguar has just unveiled the F-Type R in BLOODHOUND colours, with its sister XJ vehicle to be shown for the first time (appropriately) at the Goodwood Festival of Speed. If you’re going to Goodwood, then come and see us, and visit the new BLOOODHOUND Driving Experience on the Jaguar stand. I’ve spent a fair bit of time with the software development team in the last few weeks and the Driving Experience is going to be exactly that – a real experience!
‘Liao bu qi’ in any language
BLOODHOUND continues to excite a much wider audience than just our engineering team. I’ve just come back from China, where I was invited to by the Institution of Engineering and Technology to give BLOODHOUND lectures in Shanghai and Beijing. After much debate about national achievements past and present, we agreed that the BLOODHOUND and the Great Wall both qualified as ‘liao bu qi’ (‘amazing’).
Wherever we go in the world, there is huge enthusiasm for the way that BLOODHOUND brings science and technology to life. Right now we’ve got BLOODHOUND team members, plus a full-size Education ‘Show Car’, spreading the word at a science event in Montreal, as part of the Government’s ‘GREAT Britain’ campaign. Apparently they’ve just been visited by the Dutch Royal Family, which reinforces the impressive level of global interest.
Another race begins
As part of the BLOODHOUND Education Programme, we’ve just launched our new Model Rocket Car Challenge, with a great fun event at Santa Pod race track. There are 4 categories to compete for in the rocket car challenge, depending on how many rockets you can afford (and how long your school playground is).
The top class is the ‘unlimited’, with the current record set last year by Joseph Whitaker School in Mansfield, at an unbelievable 533 mph. I still think the first ‘BLOODHOUND’ car to go supersonic is likely to be in a school playground somewhere. May be at your local school? If so, good luck!
The Engineering Adventure continues....
As I write, a fair chunk of BLOODHOUND appears to have been stolen from the Technical Centre. The cockpit and much of the front end of the Car has simply disappeared from the workshop in the past few days. The good news is that it’s all coming back next week, painted in the distinctive BLOODHOUND blue-and-orange colours. Every week we get a little closer to being finished. There are a number of challenges still to overcome and, since this is an ‘Engineering Adventure’, that will include lots of minor problems that we don’t even know about yet. Whatever happens, we’ve got an exciting few months ahead of us.