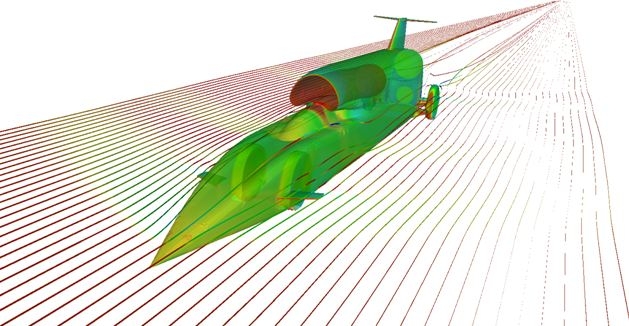
There’s so much going on at the moment that I don’t know where to begin. Four months ago we were still wrestling with a 5-tonne Car that developed 10 tonnes of lift at 1000 mph (which, from point of view as the driver, is really not a good thing). Solving this problem for a Car travelling at over 1000 mph is described by our computer modelling genius, Ben Evans, as ‘finding the Holy Grail’.
After 3 years of cutting-edge aerodynamic research, he’s right to be that excited. We’ve known for a while that we can do this astonishing 1000 mph land Speed Record – now we know how.
With this huge success behind us, the design team continues to charge ahead with the detailed design of BLOODHOUND SSC. We’re now signing up Product Sponsors to build big chunks of the Car. A major UK aerospace company (can’t tell you who just yet – they will announce it shortly) has agreed to make the whole back end of the Car.
BLOODHOUND divides neatly into 2 parts for manufacture. The carbon-fibre front end contains the hugely strong cockpit structure and the aerodynamic nose, which will endure aero loads of up to 12 tonnes per square metre at 1000 mph.
Carbon fibre front end,steel space-frame at the rear
The back end of the Car is a steel frame, which has to take the 9 tonnes of jet thrust from the EJ200, plus 12 tonnes of thrust from the Falcon hybrid rocket, plus the vibration and high temperature from both jet and rocket, plus all the suspension loads. Then, right after the thrust stops, there’s 9 tonnes of brake chute drag to deal with. How hard can that be? I expect I’ll find out, once I’m strapped into it – glad we’ve got someone really good to make the frame.
We’ve agreed the brake chutes that we want: high-speed (over 600 mph) for the desert running in South Africa and low-speed (250 mph) for UK runway testing.
Stopping BLOODHOUND SSC during runway tests – we’ll copy the RAF
The steering wheel design will be made by a process called ‘Additive Layer Manufacturing’ (the shape is literally ‘grown’ using a laser – it’s like watching science fiction). The manufacturing list goes on – you can understand why we’re excited about it.
We’re also hugely busy with full programme of public shows this summer. This Project is about education and public involvement – and that means getting out there to show people what we’re doing. I work full-time for the Royal Air Force, so mostly I’m only let out to play at the weekends. I made it to a couple of events recently,including the MACH Show at the NEC, where HRH The Duke of York came to find out more about the education programme.
Education Director Dave Rowley explains the BLOODHOUND Education Programme to HRH.
July is going to be even busier – the Goodwood Festival of Speed (where we have bragging rights on speed), the F1 Grand Prix (where we have bragging rights on power – even our rocket pump motor has 800 hp) and our biggest event this summer: Farnborough International Airshow. We will be unveiling our new, full-size (12.8m long) Show Car at Farnborough, showing the final aerodynamic shape. Quite simply, it’s stunning – the world has never seen a Car like this before.
Farnborough Airshow will also be the debut for our ‘BLOODHOUND Driving Experience’.
Developing the software for the ‘BLOODHOUND Driving Experience’ – it’s quite a ride!
Based on a driving simulator, our IT partner Intel has helped us to build the first version of a BLOODHOUND test cockpit. It gives you (and me!) the first chance to see what it’s like to drive 10 miles in 100 seconds, in a 1000 mph jet-rocket Car. I’ve been helping to develop the software and tried it again last night. It’s remarkable. Fantastically quick. And a bit scary. Come and try it for yourself…