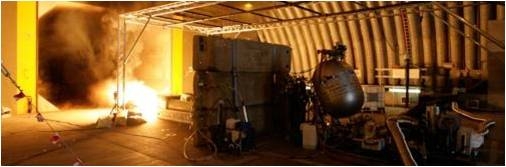
It worked – and how! Firing our hybrid rocket in public this month, with a huge international media presence and a global on-line audience, not to mention a number of our supporters’ club Gold Members, was a little nerve-wracking. This is what we had promised from day one – an Engineering Adventure that everyone could share in. The result was the first high-powered firing of our hybrid rocket, with everyone watching, when any number of things could have gone wrong. As it was, the test went exactly as we’d hoped – as hybrid ignition commenced in the rocket, a huge flame erupted from the nozzle, and we created one of the loudest man-made noises on the planet. Have a look at some of the photos here – result!
The engineering team deserves a huge amount of credit for achieving this level of performance in our first-ever pump-fed firing. The only previous test of the rocket had been 3 years ago, at an isolated test facility in the US, and at a very low pressure (300 psi, or 20 Bars – 20 times atmospheric pressure).
Rocket pump by Cosworth
This month’s firing was the first test using the high-speed pump, driven by a Cosworth Formula 1 engine (yes, really – at full speed, the pump will need some 800 hp to turn it, and the Cosworth engine is the smallest 800 hp pump motor that we could find!). Our target for the test was a massive increase in pump pressure, to 800 psi – we’d initially discussed 600, but when we looked at the detailed plan, the team was confident that we could deliver more, so we aimed high.
The rocket system was set up inside one of the old cold war hardened aircraft shelters at Newquay airport. The firing team was set up in another of these big concrete hangars, 200 metres away – so everything had to be controlled remotely, using very long cables and monitoring the rig through video cameras.
There were some small delays on the day (rocket tests rarely run on time, whether you’re NASA in Florida or Bloodhound in Newquay). Our major problem was trying to keep the F1 engine warm. The tolerances in the F1 engine are so tight that the engine cannot be started unless it is already hot. The October weather in Newquay was cold, and even with the engine’s electric heaters running flat-out, we couldn’t keep the Cosworth engine warm enough. When the engine is in the Car, it will be enclosed and easy to keep warm (the problem will be keeping it cool once it starts up!), but on the test stand, it was getting cold very quickly. Shutting down the ventilation fans and keeping the doors almost closed did the trick. The wind was no longer blowing over the engine, the temperatures started to increase again, and we were back on track for the firing.
And the blast will go out here.....
At T minus 5 minutes, we started to show our new video animation of the rocket to the hundreds of media and other guests at Newquay. The audience included a number of our Supporters’ Club Gold Members, so if you want to come and see a future event, or come and see the Car being tested in the UK next year, join the Club! Thanks to Cisco, we streamed the firing live to a global internet audience of over 100,000. Our new website also had a good workout – over 227,000 pages in one day. If you haven’t seen the new Bloodhound website, go and have a look round – our webmaster, Nick Chapman, has done a fantastic job.
As we started the video playing, the rocket test team started their final 5 minute countdown, including clearance from Newquay air traffic control. At 2 minutes to go, as the video finished, the F1 engine started up, idling at a racy 5000 rpm for its final warm-up. With less than a minute to go, the Cosworth engineers blipped the throttle to confirm that the engine was ready, then handed control over to Bloodhound. The high test peroxide (HTP) tank had been pressurised to 1.7 Bar (25 psi) and 400+ litres of HTP sat ready in the tank.
To start the firing process, we used an igniter inside the rocket – the high-tech equivalent of ‘a sock soaked in petrol’ (to quote our PR team). On the video of the firing, you’ll see the initial burst of flame this produced. The Cosworth engine then ramped up to 8000 rpm as it started to turn the pump. The high-pressure valve opened by 10% and the HTP started to flow into the catalyst pack at the end of the rocket. 80 layers of silver oxide mesh broke down the HTP (hydrogen peroxide – H2O2) into water (H2O) and oxygen – and released a lot of heat. After a few seconds the catalyst pack was approaching its operating temperature of 600 deg C – at which point the hybrid rocket fired up! The engine rapidly accelerated to 16,600 rpm, delivering just over our target feed pressure – 41 Bar (820 psi). A huge bright orange flame lanced out from the rocket, creating a massive storm inside the firing hangar. This howling gale knocked over cameras and blasted every scrap of loose material and dust out through the exhaust vents – and 200 metres away, sealed in our own concrete shelter, we felt the ground tremble.
The rocket fired for 10 seconds, burning up all 400 litres of HTP. At the end of the firing, flames continued to lick from the rocket nozzle, until the control team fired bursts of high-pressure nitrogen through the system to quench the flames. Shutting the rocket down quickly is one of things that we’ll work on during future firings – I don’t fancy finishing every high-speed run with the back of the Car on fire!
The rocket firing generated the loudest man-made noise on the planet that day, so I’m told. This level of sound energy may be enough to damage the back end of the car, so this is one of the things that we tried to test. We put carbon fibre panels either side of the rocket nozzle, where the rear wheel fairings will be, to see how they would cope. Unfortunately, we don’t know the result, as they caught fire at the end of the test....
This wouldn’t happen in the Car, as the panels will have up to a 1000 mph of cooling air flowing over them. However, we’ll have to find a different way to protect them during test firings.
6.5 tonnes of thrust – just testing
Initial results show that we delivered about 6.5 tonnes of thrust, which is exactly what we were expecting. A perfect result. The rocket is now being stripped down to examine all the components in detail – this was an experimental firing after all. The other really good piece of news is the equivalent performance we will get from the ‘monopropellant’ mode of the rocket, using HTP alone without the solid rubber fuel. For 2013, we are aiming for 800 mph, which will require the monopropellant rocket to deliver at least 3.5 tonnes of thrust. Based on the figures from this month’s firing, the Cosworth engine and pump should comfortably deliver at least this much thrust. We can fit this system into the Car for next year, while we run a separate test programme to develop the full 12 tonnes of thrust for the hybrid rocket, which is what we are going to need to reach 1000 mph in 2014. All in all, a great result.
For a short video summary of the whole event, have a look at our latest instalment on Cisco Bloodhound TV: episode 17 – Hybrid Rocket Test.
Precision machining of a 1000 mph cockpit
Work on the rest of the Car is coming on well. The lower rear chassis (an all-metal structure) is being assembled by Hampsons, while the design work on the upper chassis, which has to support the jet engine as well as the fin, is mostly complete. Incidentally, we’ve now got over 13,000 names on the Fin – and if you want to your name to travel at 1000 mph, there’s still room! The carbon fibre monocoque, the one-piece front chassis structure which includes the cockpit for the Car, is still being worked on. It looks like we’re still on track to bolt the bits together before the end of the year. Having the chassis in one piece for the first time is going to be a great Christmas present for all of us.
We signed an agreement this month with Minister for Defence Equipment, Support and Technology, Philip Dunne MP. This ‘concordat’ (Government word for ‘agreement’) recognises all the work we’ve done together so far, including the loan of the EJ200 jet engine, the MOD graduates that have been training in the Bloodhound design office, and the joint work that Bloodhound and the MOD have done to develop the UK’s rocket design capability. We have been joined by a small group of technicians from the Royal Electrical and Mechanical Engineers – the British Army’s technical experts.
The MOD supports Bloodhound
(picture: Crown copyright)
They are going to help with the build and running of Bloodhound over the next 2 years, while developing their own skills by working on the full range of Bloodhound’s cutting-edge technologies. Our Education Programme has reached over 5300 schools and colleges in the UK so far – and now it includes the British Army as well.
I also got a chance to take part in another world record this month. The charity ‘Aerobility’ ran a fund-raising record event, aiming for the longest simulator flight ever. The charity’s aim is to inspire people by giving them a chance to fly, and then to ask ‘if I can do this, what else can I do?’ As a fighter pilot, I can relate to this approach – it works.
I get my co-pilots from eBay
In order to break the existing 7-day (168 hr) record, the team was going to fly a light aircraft simulator (a PA-28 ‘Warrior’) around the world in 10 days, setting a new 240-hour record in the process. They got an amazing list of ‘pilots’ to help out as well. DJ Chris Evans, astronaut Buzz Aldrin, head of BA Willie Walsh, head of the Royal Air Force Sir Stephen Dalton, and of course some guy that drives very fast. I offered to fly a leg towards the end of the event – which to my surprise turned out to include the 168 hr mark, which broke the old record. I think they enjoyed the irony of this being my slowest-ever world record event....
I can’t claim all the credit though – my excellent co-pilots Sarah and Steve (2 very generous winners of the eBay auction) did all the work, while I did the captain thing of sitting there supervising! As I write this, the challenge is just coming to an end – a great effort and a good cause. For the final result (and a chance to donate) have a look at the Aerobility Global Flight Simulator Challenge website.
Finally, I’ve just come back from the US, where I’ve been test-driving a Bentley on the Bonneville Salt Flats, as part of a short film on ‘The Future of Speed’. We got the Bentley Mulsanne, a 2.7 tonne monster of a luxury car, up to 191 mph – the fastest that it has ever been, and not bad for a standard road car! Speed is something that fascinates human beings and, in one form or another, always will.
190 mph coming right up
Speed in the future will be limited by 2 things – technology, and the will and passion to use it. Ultimately, this is what Bloodhound is all about. We want to inspire the passion to embrace the technologies of the future. The people who will build and live in the high-technology low-carbon world of tomorrow are at school right now – and following Bloodhound in their millions. The Bloodhound Education Programme is making a difference to the way they think about science and engineering, and that is a great investment in the future.