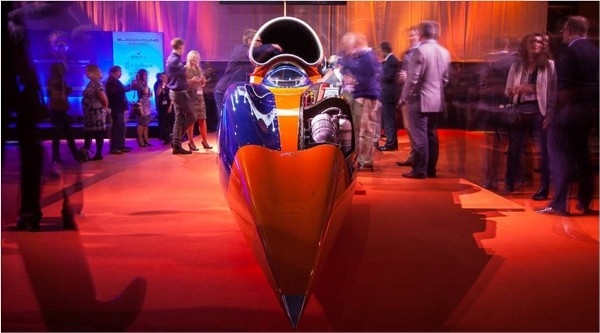
Finally, the news we’ve all been waiting for. We’ve just confirmed a new source of funding, so we can now crack on with getting BLOODHOUND SSC ready to run. It seems like a long time since we launched the Car at Canary Wharf last September, and completing the funding package has taken longer than we’d hoped, but we’ve got there. More details to follow shortly – watch this space.
Plenty of work to do
The first task for the BLOODHOUND team now is to work out how quickly we can get everything completed. There are perhaps 4 major groups of tasks for us to plan: we’ve got to get the Car ready to run, complete the rocket system development, finish the desert preparation and do the UK runway testing. Only when all 4 of those are completed can we go to South Africa to start testing the Car, working up to a new World Land Speed Record and ultimately on to 1000 mph.
The obvious first step is taking the Car from last year’s ‘dry build’ stage to ‘ready to run’. There are hundreds of different areas that all need finishing off and testing, including chassis structure, suspension, fuel systems, sensors, computer software, electrical power, hydraulics, video cameras, bodywork….. the list goes on, and on, and on. Sequencing all of these jobs is our first task and we’re working on it right now.
The second work package is the rocket motor. BLOODHOUND is powered by perhaps the best military jet engine in history, the EJ200 from the Eurofighter Typhoon. However, we are planning to go faster at ground level than any jet fighter, ever, which is why even this remarkable supersonic engine won’t get us all the way to 1000 mph. To achieve the big number, we need the Nammo rocket system as well. This will add approximately 120 kN (about 12 tonnes) of thrust, more than doubling the power output of the Car. However, for our first tests (up to around 800 mph) we need less than half that thrust. To keep it simple, we will start with a ‘mono-propellant’ rocket, using just the High Test Peroxide (concentrated H2O2), without the rubber fuel element of the hybrid rocket. This will test the rocket control systems in the Car, and it will give our rocket team more time to refine the prototype hybrid rocket, before we need it for the attempt at 1000 mph. Using the monopropellant rocket for our first year of running is an engineering compromise where everyone wins.
Track preparation
The third task it to complete the desert preparation. The Northern Cape Government team has done the most amazing job of clearing the desert surface, removing 16,000 tonnes of stones from 20 million square metres of surface. After the track had been cleared, we completed a laser scan of the track surface, to make sure that it was flat enough for the Car to run on, and to give us some idea of what the Car’s suspension will have to cope with. While the track is mostly ready, there are still some small areas to fill and grade, so that needs doing quickly.
Team Manager Martyn Davidson has been working for a long time now with the Northern Cape Government and the South African security services, to make sure that we can run the Car safely with thousands of South Africans watching (more likely tens of thousands, every South African I’ve ever met is planning to come). On top of that, there’s all of the foreign tourists who are going to visit. If you want to come and watch the race to be the fastest car on earth, then keep an eye on our Hakskeen Pan update page for more details, or join the 1K Club to receive regular updates.
Newquay International – a 9,000 foot test track
The fourth task from my point of view is the UK runway testing, which will be done at Newquay Aerohub (want to come and watch the tests? Join the 1K Club as a Gold Member and we’ll see you there). Before we deploy the Car and team 5000 miles to South Africa, we want to make sure that everything is working properly. That doesn’t just mean the Car, it’s also testing all of the support equipment, including towing the Car, refuelling it, checking the data systems, etc.
We’re aiming to let you watch the video and data from BLOODHOUND, online, while the Car is running, so we’ll be testing the transmission systems at Newquay. UK running will also allow us to train the team. The engineers may be capable of building the most advanced straight line racing car in the world, but we also need to learn how to run the Car safely in a desert 5000 miles from home. It all takes careful preparation.
Once all of this preparation is complete, we can finally start testing the Car at high speed. In designing the world’s first 1000 mph car, we’ve already conducted some of the most advanced computer modelling in the history of the Land Speed Record. This research is only half of the story though, as we still need to prove the results in the real world, and refine the bits that the computers can’t model accurately.
Checking the details
The most important element of the test programme is going to be validating the aerodynamic model. In other words, we need to make sure that BLOODHOUND’s unique ‘lift-neutral’ shape works exactly as we want it to. We’ll take the Car to supersonic speeds in carefully controlled steps (the speed of sound is around 760 mph, which is why we’re aiming for 800 mph initially), to check the aerodynamics in detail. The aerodynamic forces are absolutely huge, with a ‘stagnation pressure’ of almost 12 tonnes per square metre at 1000 mph. If you put your hand out of the Car window on the motorway, the ‘stagnation pressure’ exerts a force equating to about half a kilogramme. Put your hand out of the window at 1000 mph and the load is more like quarter of a tonne, so we need to check the loads across the whole Car very carefully.
The other key thing is to find out exactly how much drag we will have at supersonic speeds. We really are working at the limit of computer modelling, as there is no precise way to calculate the drag on BLOODHOUND in the turbulent air at the back of the Car, at supersonic speeds. We’ve got the best estimate that science can provide, so now we need to go and measure it precisely. This drag measurement will then define exactly how much power the hybrid rocket has to produce, in order to get the Car to 1000 mph.
Exploring BLOODHOUND – the App
IIf you think that all of the above sounds like a long and complicated list of engineering tasks, then you’d be right. We’ve tried to simplify it a bit by creating a new BLOODHOUND App (download it here), explaining the key elements of BLOODHOUND’s engineering and technology in more detail. Enjoy.
While we’re working away at the ‘big’ car, the BBC micro:bit model rocket car competition is reaching its climax. This amazing competition is exciting and inspiring young ‘engineers’ all over the country, with thousands of teams taking part in this epic event. By the time you read this, the Scottish finals will have been completed, with the finals south of the border to follow at the start of July.
It’s great for us to see BLOODHOUND education already delivering such a powerful and inspiring effect. I’m excited by the thought that we’re finally getting BLOODHOUND ready to run and, judging by the thousands taking part in the rocket car competition, I’ve got a lot of company. Keep watching boys and girls, we’re on the way now!