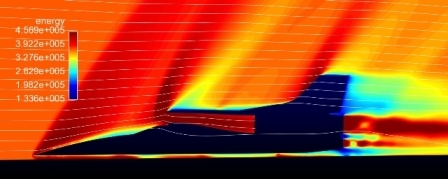
Following last month’s hugely successful rocket firing, we’ve been thrilled by the very high levels of international interest. In the first 48 hours, we ran over 300,000 pages on our website and over 6 million views on YouTube. I can’t wait to see what happens when we start running live video from the Car next year....
Rocket Fuel Grain – Before and After
We’re still analysing the data from the rocket firing but it turns out that we got even more than we bargained for. The fuel grain (Hydroxyl Terminated Polybutadiene for the chemists out there, solid rubber to the rest of us) was breaking up at the end of the firing, as you can see from the before and after photos. At the heart of a live rocket firing there is a screaming inferno of gasses at over 2500 deg C, and the fuel grain insulates the rocket casing from this searing heat. As the fuel grain broke down, the metal rocket casing started to overheat – and was just moments from an uncontained failure (i.e. explosion!) when we shut the rocket down.
So does this mean that the test failed? On the contrary, this is exactly the sort of information that we needed. The test programme is designed to push the prototype rocket to its limits and to find any weak points, so that we can improve it wherever we need to. Initial analysis suggests that the failure probably occurred at the ‘step’ in the fuel grain, between the star-shaped main body and the round tail end. Removing this step in the casting is a simple job and should fix the problem – make sure that you watch the next test to find out! If you missed last month’s firing, there’s a great summary of it in the latest episode of Cisco Bloodhound TV.
The rocket programme is now undergoing an independent review, to check progress so far and to optimise the rest of the programme. This will deliver the full hybrid capability for the 1000 mph runs in 2014, with an interim monopropellant rocket in 2013, which is already well advanced. The monopropellant system uses our Cosworth F1 engine to pump high test peroxide (concentrated H2O2) through the silver oxide catalyst pack, breaking it down into high-temperature oxygen and steam. This high-pressure gas stream is then fed directly out of the rocket nozzle (no solid rubber fuel) to generate around 4 to 5 tonnes of thrust – which should be enough to reach 800 mph next year.
The supersonic technique is like this....
Last month I was lucky enough to see the Cosworth engine in its ‘natural’ habitat, in the back of the HRT F1 car. As a late birthday treat, I went to the Indian Grand Prix and ended up in the pits, looking round the HRT garage and talking to Indian driver Narain Karthikeyan.
It was great to find out that Bloodhound is being closely followed out in India as well – especially at HRT, as one of their Cosworth technicians had recently helped us to set up last month’s UK rocket test. The Bloodhound Education Programme is also being promoted in India, with the Times of India writing about Bloodhound in an education supplement that goes to 850,000 schools across this huge country. I suspect that the audience for BLOODHOUND is going to be vast just in this country alone, never mind the rest of the world.
View from the front left winglet camera
I was part of a fascinating meeting last month to discuss camera locations, and how we are going to get the video signal off the Car and onto the web. We are planning around 16 media cameras in and around BLOODHOUND, ranging from (F1-style) HD cameras in the cockpit to miniature mobile-phone cameras embedded into the winglets, wheel fairings, etc. We will be able to transmit any 3 channels live onto the internet, so that you can follow the run from a range of views.
But hang on a minute – we’re in the middle of a desert, doing a 1000 mph. How are we going to get 3 camera feeds, plus my voice and lots of data channels, off the Car and onto the internet from there?
In answering this we are really grateful for the fantastic support of our Product Sponsors. MTN is erecting a series of 60 metre masts, using LTE technology (like 4G), with some help from Plextek. One of the masts is 16 km out to one side of our track, to reduce what is known as ‘Doppler shift’ – the change of frequency that occurs with speed (this is the effect that you hear when a racing car passes you and the engine note appears to drop – the same thing happens to radio signals, and the change in frequency doesn’t help with data transmission!). Being 16 km away, Bloodhound will also remain in one ‘lobe’ of a mobile phone antenna during the whole run, so we can transmit continuously along the whole track without any breaks. Fit large sideways-facing aerials into the Car, turn the gain (the ‘volume control’) right up, and it’s job done.
So (like many other things in our ‘Engineering Adventure’) there will be a lot to discover and some problems to solve. But that’s why we’re here and difficult is what we do – and the end result, live video at 1000 mph, is going to be amazing.
While the external shape of the Car was fixed some months ago, work continues on improving our modelling. The aerodynamics team at Swansea, under Dr Ben Evans, are just starting to use a new computer network called ‘High Performance Computing Wales’. HPC Wales is a network of super-computers that will give us, to quote Ben, ‘virtually unlimited’ computing resource. That will allow us to do some more accurate airbrake simulations and to refine the design. Ben is also learning more about the body shape that we are now building, looking at the differences in airflow with the EJ200 jet engine on and off, and the airflow and stability of the Car at 2 degrees of yaw. There are any number of reasons why the Car might get off line by 1-2 degrees (have look at ‘Steering Bloodhound' for more detail) and we need to know that the Car is safe, even if I can’t keep it perfectly straight all the time!
Bloodhound Composite Engineer Stuart tries out the cockpit for size
Work on the chassis continues, with the lower rear chassis being delivered to our Technical Centre in Bristol this week. The front monocoque/cockpit moulds are complete and we’ve already received a fibre glass ‘splash’ (test piece) from URT, before they get on with completing the final carbon fibre components. These ‘splashes’ will be used to fit out the cockpit internally, so that when the carbon monocoque is completed, we can simply transfer all of completed components (instrument panel, seat, harness, steering wheel, pedals, etc.) into the real cockpit.
Castle Precision Engineering has now completed the machining of our runway wheels, which will be fitted with high-speed aircraft tyres for our tests in the UK next summer, taking the Car up to around 200 mph (the exact speed will be determined by the brake energy capacity).
UK Runway wheels – testing starts in 2013
If you want to come along and watch some of Bloodhound’s first test runs, then join our Bloodhound Supporters’ 1K Club – it’s a one-off payment for the lifetime of the Project, so the earlier you join, the more value you get.
Our new Mission Control Centre
As if all this activity wasn’t enough to keep us busy, we’re also moving. The Bloodhound Technical Centre in Bristol has been a fantastic home for the past few years, but as all of the hardware and support vehicles start to arrive, and we start the assembly of Bloodhound SSC, we need somewhere bigger. Subject to contract, we should be moving by Christmas, which is just as well – we’ve just been promised a trailer for our Mission Control Centre and we need somewhere to keep it!
History in the Making
The final bit of good news – and it’s a huge bit – comes from our track at Hakskeen Pan in South Africa. After a truly remarkable effort, the Northern Cape team has now virtually completed the stone clearance and track preparation, including the removal and grading of the old causeway. No-one has ever attempted this scale of work on a high speed track before (except perhaps for Malcolm Campbell, back in 1928/29, also in South Africa) so it has been a huge technical challenge. With no previous experience to draw on (none of the current team were around in 1929!) our Track Boss Rudi, the Northern Cape project manager Nico, and the 300+ local workers have had to develop the best methods as they went along. The final result is just brilliant – have a look at Rudi’s latest desert update, ‘History in the Making’ to see just how good. Having shifted nearly 6000 tonnes of stones by hand, they really are creating the world’s best race track for us.