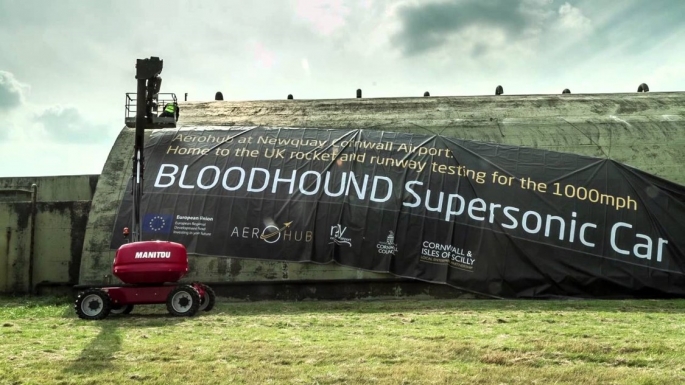
After some intensive planning, the target date has been chosen. BLOODHOUND plans to set a new Outright World Land Speed Record, aiming at 800 mph, in October 2017. The announcement video doesn’t give you any clues on the identity of the new sponsors, but it won’t be long, as they’re planning a big announcement in a couple of months’ time.
Following this announcement, BLOODHOUND is now getting ready to go racing, which sounds like a fairly straightforward job. First, we need to take the ‘dry build’ Car apart so that we can finish the electrics, hydraulics, and so on (this is your last chance for a few months to come and see the fully-assembled Car). Once all of the systems and structures have been finished off, we can re-assemble the Car and take it somewhere long and flat, and I’ll jump in and start it up for the first of a number of test runs. Supersonic here we come.
First step, take it to bits
In simple terms, that’s the engineering task over the next few months. Of course, we’ve got to coordinate this with a lot of the 250+ sponsor companies who are helping to create the world’s first 1000 mph car. We also need to make sure that we’ve got the right engineering expertise on the team at each stage of the design, build and test process.
Of course, the engineering plan is only a small part of the task. We’ve got to take the Car to a dry lake bed to run it supersonic, which means shipping everything overseas. We’re very lucky to have the superb hand-cleared track waiting for us on Hakskeen Pan in the Northern Cape of South Africa. This means shipping the whole Project to South Africa, to allow us to prepare, test and (if necessary) modify the world’s fastest car in the middle of the desert, 5000 miles from home. Oh, and we also have to feed and house 50 team members, plus a number of embedded media.
The scale of this task is fairly daunting. We’re aiming to sea-freight as much of the support equipment as we can, with technical workshops, an electronics workshop, a composite repair shop, a rocket preparation workshop and a couple of the specialist support vehicles all going by sea in shipping containers. The total is about 15 containers, containing around 100 tonnes of freight, to be shipped to one of South Africa’s ports, then driven about 700 miles cross country to Hakskeen Pan.
Newquay getting ready for us
While all of this is in transit (it will take about 6 weeks to get there), BLOODHOUND SSC will be down at Newquay Aerohub, doing its initial ‘slow speed’ (200+ mph) test runs. That means we’re going to need enough support equipment to run the Car, including refuelling rigs, rapid response (safety) vehicles, road trailers, spares, etc.
Once the UK testing is complete, we’ll fly the Car out to South Africa, as that’s the quickest (and, for ‘delicate’ things like jet engines, the best) way to get there. We’ll need to take all of the UK support equipment with us as well, so that we’re ready to run when we get there. That gives us about 95 tonnes of air freight, on top of 100 tonnes of sea freight. Just from the numbers, it’s obvious that running a supersonic jet-and-rocket car, in a desert, is a massively complicated engineering and logistics task.
One small part from Massachusetts
The huge quantity of equipment is not the really difficult bit, though. A lot of our equipment is ‘categorised’, which means that its use and movement is limited by one (or more) international treaties. For example, if we are going to export any defence-related US technology to a third country, we need permission under the US International Trafficking in Arms Regulations, or ITAR. To consider just one item, our Eurojet EJ200 jet engine is the best military jet engine in the world, so it’s definitely ‘defence-related’. As the name would suggest, the Eurojet is made in Europe. However, if you read the full list of parts in the EJ200 you’ll find that, for example, the oil temperature probe in the engine was made in Massachusetts.
It doesn’t matter if every other component of the EJ200 is European – ITAR applies, and getting US State Department clearance is not a quick process. We prepared a list of every single ‘defence-related’ BLOODHOUND component nearly 2 years ago, and submitted it to the US State Department, so we’ve now got ITAR clearance.
Small pump, big paperwork
That’s only the start of the paperwork. BLOODHOUND has a rocket motor, so the Missile Control Technology Regime (MCTR) applies. Obviously we’re not going to build anything resembling a ballistic missile, but this is technology that could be misused. We’ve done a lot of work over the past 2 years to show that we will be using the rocket ‘properly’ and that we will look after the technology. In addition, we also need to meet various national UK and South African regulations, plus the international ‘Wassenaar Arrangement’ that controls the export of conventional arms and ‘dual-use’ technologies. This is where it gets even more complicated. A lot of the cutting-edge technology in BLOODHOUND, ranging from the computers to the stainless steel pipework for the rocket, could be ‘dual-use’, so this covers an awful lot of what we own. Indeed, some bits of the rocket system are controlled under ITAR and MCTR and Wassenaar.
Not put off a record attempt yet? It gets worse. When we get to South Africa, we are going out into a remote and beautiful area of the Kalahari Desert. We’re going to live and work out there for a number of weeks, so we need to make sure that we meet all of South Africa’s environmental and commercial legislation. The National Environmental Management Act, the Safety at Sports and Recreational Event Act, the Public Financial Management Act, the Municipal Financial Management Act, the International Government Relations Act…. the list goes on. The compliance paperwork that we’ve completed over the past few years is about a metre tall, if you stack it all in one place.
Hakskeen Pan – a supersonic river
Some of these regulations can be unusually complicated for a Land Speed Record like BLOODHOUND. For example, we are running on Hakskeen Pan, which is a dry lake bed. The lake bed floods occasionally, which is a good thing, as it makes the surface wonderfully smooth. However, the flooding means that legally it’s considered to be a water course, just like a river, which has made the environmental application process more difficult. As one of the lawyers pointed out when we started this process: ‘In legal terms, you’re applying to run a supersonic car down a river – and the legislation was not drafted with that in mind’.
Finally, I’ll mention one more set of requirements while we’re on the subject, namely Health and Safety. In fact not just one set of H&S legislation, but two – as a UK team we have to follow a lot of UK H&S rules, and as we’re running the Car in South Africa, we have to follow South African H&S rules as well. We’ve always said that we would run the Car as safely as possible, but I don’t think doubling up on H&S paperwork was quite what we had in mind.
Thanks to Team Manager Martyn
Thanks to a huge level of support from subject matter experts in the UK, the US and (mostly) in South Africa, we’re on top of all of these requirements, and many others. This represents a massive effort by our team manager Martyn Davidson to bring it all together, so if you see a slightly worn-looking scotsman at a BLOODHOUND event in the near future, please tell him ‘well done’. When BLOODHOUND and all of its support equipment arrives in South Africa next year, with legal authority to run on Hakskeen Pan, it will be directly thanks to him and his team.
Looking at all of these problems, it’s tempting to wonder why anyone ever tries to do something like this. It has taken years of work to get ready to ship the Car and the team to South Africa, and we will have to repeat the whole process a couple of months after we get there, when we re-export everything back to the UK. If that wasn’t enough, we’ll arrive back in the UK after setting a new supersonic World Record, do 9 months of engineering work (to prepare the Car for 1000 mph), and we’ll then go through the export/import process all over again for our second visit to South Africa. Looking at this massive (and largely thankless) task, there’s one obvious indication that we’ve got the right kind of people to achieve this epic ‘Engineering Adventure’. Despite the enormous challenges ahead, we can’t wait to get started.