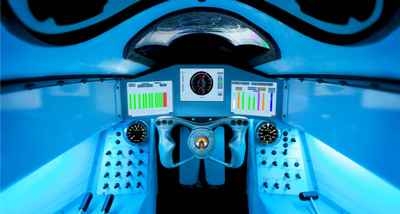
It was great to see the cockpit finished and unveiled in public this month. This is my ‘1000 mph office’, which I first started to design over 6 years ago. It’s been exciting to see it come together, but as the design of the Car became more detailed, I’ve had to change some of the requirements as we went along. I’m thrilled and – I can now finally admit – slightly relieved that it does all fit in the space available.

The design approach for the cockpit was a simple one. I need to see over the nose (so that I can see where I’m going!) so that fixes my eye height. With large acceleration and deceleration forces, I want to sit as upright as possible, so the seat sits right down on the cockpit floor. The centre cockpit display screen needs to be just below my eye line, so I can easily scan between the track and the speedometer, etc. The steering wheel needs to be low enough to see the screens over it. My legs need to be fairly straight, to keep clear of the bottom of the steering wheel, so the pedal box is as far forward as possible, while the seat is as far back as possible,
Five years ago, we built a cockpit mock-up to make sure that everything would fit. Once the mould for the cockpit outer shell (the carbon fibre ‘monocoque’) was complete, we made a second mock-up from this mould, to refine the position of the seat, windscreen, instrument panels, and so on. Then the huge load-bearing sills inside the cockpit were added, reducing the room for instrument panels, The internal handle over my head for the cockpit hatch was added, reducing the headroom available. The rear cockpit bulkhead grew a ‘bulge’ to fit the huge HTP tank fitted just behind the cockpit. All of this was drawn in the 3D computer model, and appeared to fit – just – but there’s only one way to be sure. Hence my relief last week when it all came together and showed that it all does fit – just.

Once all of the hardware was in position, the final job was to mould the seat around me. The seat starts as a huge plastic bag full of polystyrene beads, essentially a large see-through bean bag. Once we’ve got the volume of beads right, they are mixed with an epoxy resin. Now the pressure is on, as I have to sit in the bag, mould it to my shape, make sure I’m in exactly the right position, and then sit very still for 30 minutes or so while it starts to set. The bag is under vacuum to keep it fairly solid, but it’s still easy to move and distort the shape, and I’ll be stuck with the result for the next 2 years so it needs to be right. I’m pleased to say that my new friend Vaughn from Real Equipe did a cracking job and it fits perfectly.
Once the seat was set, we used our Hexagon laser scanner to update the computer model of my sitting position, and then (once I’d climbed out of the now-solid seat bag) we scanned the surface of the seat. In the final part of the process, this seat scan is used to produce a carbon fibre seat shell in exactly my shape, which is then solidly mounted into the cockpit structure. We’ve been working closely with the FIA Institute to refine the cockpit design and there is a clear safety advantage in using in a solid carbon seat. This was a slight surprise to Vaughn, as he was originally hoping to stop at the bean-bag stage, which is what many race cars use. Sorry Vaughn!

The cockpit has to perform 3 different functions. Firstly, it has to protect me. The carbon monocoque took some 10,000 hours to design and build, with huge thanks to URT, SHD and co., who have produced a world-class product. The result is a 200 kg box which is probably the strongest safety cell in the history of motorsport. It has to protect me from the aerodynamic loads at 1000 mph, which are up to 12 tonnes per square metre: that’s the weight of 3 elephants standing together on the bonnet of a small car.
The second job for the cockpit is to provide me with all the instruments and controls that I will need to control the world’s fastest Car. A steering wheel (6 buttons for chutes, airbrakes, radio etc., and 2 triggers for the rocket systems), 2 pedals (right foot accelerator – but unlike your car, this one has a Typhoon jet engine attached to it – and a left foot brake pedal for the wheel brakes), 3 multi-function screens, the Rolex independent speedometer and chronograph, 34 switches and buttons, and 3 back-up levers in case of system failures. To make that easier to understand, have a look at our video tour of the controls and the 360 degree photo view of the cockpit.
Why so complicated? Well, I could just have a large ‘ON’ button and another one labelled ‘STOP’. However, as we start testing BLOODHOUND next year, we are going to want to check every system in turn, and possibly change the way they are set up between runs. Easy to do with cockpit controls, not so easy to do without. That’s why it looks a bit like a jet fighter inside: we need to be able to control each bit separately.
Finally, the third job for the cockpit is to be the centre for the world’s fastest outside broadcast studio. Our long-term goal is to bring science and technology to life for a new generation of young engineers. To do that, we’re going to stream live in-cockpit video, and technical data, through the internet every time we run BLOODHOUND. The aim is that wherever you are in the world, you can watch exactly what we’re doing, live.

The key to streaming live video from a Car doing 1000+ mph, for the first time in history, is the new MTN mast network surrounding our track on Hakskeen Pan, in the Northern Cape of South Africa. We’re very lucky that MTN has made this huge investment in our ‘Engineering Adventure’ as this will allow us to share it live with a global audience.
The only downside is that I’m going to have tens of millions of people looking over my shoulder and marking my homework in real time, but I suspect I’ll be far too busy to worry about it.
The end result is a purpose-built cockpit which will do all of these jobs perfectly. As a bonus, it’s comfortable to sit in, but that will change when Car starts running. With the EJ200 military jet engine screaming behind my head, the high temperatures of a sealed cockpit in the desert, the chassis vibrations from the jet and rocket, and the high G forces, it’s going to be a physically demanding experience.

Right now my major concern is the noise in the cockpit, as we don’t know quite how loud it’s going to be. The good news about going supersonic is that I won’t be able to hear the jet engine any more (it’s behind me and I’m going faster than the sound waves it’s making). The bad news is that we expect the supersonic shock waves over the cockpit to be even louder than the jet.
At maximum speed, the air just in from of the cockpit is hitting the Car at over 1000 mph. Just behind the cockpit, the air is entering the jet intake at about 600 mph. Hence the shock waves over the cockpit are designed to slow the air down by over 400 mph in just over 1 metre. In aerodynamic terms, that’s a crash-stop, and it will generate huge amounts of energy just over my head. We’re going to put a lot of sound insulation into the cockpit, but I’m not sure it’s going to be enough....
Another major step forward this month was the spin test of the desert wheel. The wheel is a solid aluminium disc, about 91 cm in diameter and weighing some 95 kg. At maximum speed, the wheel will spin at over 10,000 rpm – 170 times per second – and the wheel rims will experience an outward acceleration of 50,000 times the force of gravity. 50,000 radial ‘G’ is why they are made from solid forged aluminium, as there is no tyre in the world that can survive that kind of load.

The wheels were forged by Otto Fuchs last year (if you haven’t seen it already, have a look at the video of the process, it’s fascinating). These incredibly strong discs, known as ‘cheeses’, are then machined by Castle Precision to the very precise shape that Lockheed Martin (UK) helped us to develop. All well and good, but at high speeds the wheels are safety critical, so how can we prove that this unique design will cope? Step forward Rolls-Royce, who gave us the use of their engine spin test rig
We spun the wheels to 10,496 rpm. Strange things happen at these speeds. The wheel grows very slightly under the 50,000 G load (it was this growth that we were measuring). It also gets quite warm. Above 6000 rpm, the wheel was heating up by one degree per second, peaking at 92 degrees C. The good news is that wheel behaved exactly as we expected, so it passed the test.

With the wheel shape proven, Castle can manufacture the rest of our desert wheels for 2015. All we need now is the rest of the Car to bolt them to, and that’s coming along very nicely. In addition to the cockpit, the upper chassis panels are now almost complete, Timken has supplied all the steel wheel bearings (3 per wheel, in matched sets) for our runway tests, we’ve received all 200+ bits for the airbrake systems, the jet engine fuel tank (a marvel of carbon fibre complexity) has been delivered, and vehicle assembly is pressing ahead. Next year’s test runs in 2015 are starting to feel closer all the time.