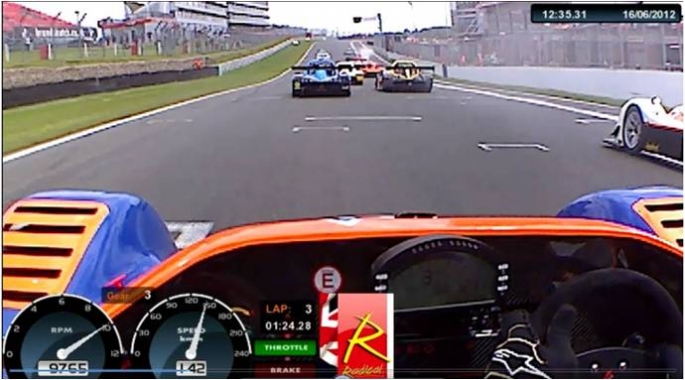
Richard Noble has just returned from South Africa, where he’s been catching up on the desert preparation and finalising some new sponsorship for our 1000 mph record attempt. The Northern Cape Government team is doing a fantastic job of clearing the world’s best race track for BLOODHOUND – after the last rainy season, the surface is in great condition and with the stones removed, it’s now looking terrific.
Richard and the track team
The remnants of the old causeway, which used to run across the desert, are being re-graded to improve the surface still further. This surface grading is an exacting process, as it is easy to damage the surface. It’s also an unusual one, as most dry lake beds come without causeways, so we are in slightly uncertain territory. Still, with the Northern Cape team on the case, we’re on course to have the perfect track by the time we run there next year.
Project Manager Nico Fourie – seeking perfection
We have no real idea how many spectators we will have when we’re out in the desert in 2013. South Africa is vast – Richard drove a 2300 km round trip from Johannesburg – but everyone I met in South Africa last year was adamant that they would be there to watch. However, if we are going to create a truly global ‘Engineering Adventure’ then we need to make sure that everyone can watch BLOODHOUND SSC run.
We’ll be transmitting live data and video from the Car every time it runs, so that you can watch the event wherever you are – but first we need to get the data and video from the Car to the internet. We’re thrilled that Richard signed a deal last week with South African telecoms giant MTN, who will provide the ‘back-haul’ link from the desert to Upington, some 200+km to the south (the nearest internet fibre-optic link). With this deal in place, we really can let the whole world share in the Adventure.
The design and build of the Car is progressing well. BLOODHOUND designer Mark Elvin has been working closely with Hyde engineering to complete the design of the upper rear chassis and fin structure. This is one of the last major bits of chassis to design and Hyde is proving to be a great partner for us. They’ve been pestering us for ages to get started with fabrication, so finally we’re keeping them busy.
Keeping the Car pointy-end forwards
We need to make sure that the Car will stay ‘pointy-end forwards’ by keeping the aerodynamic centre of the car behind the centre of gravity. The rest of the design needed to be mostly complete before we knew where the centre of gravity of the Car would be, and hence how big the Fin would need to be: the bigger the Fin, the further back the aerodynamic centre is. This is the last piece of the puzzle and we’re just about ready to start making it, which is great. If you’ve already put your name on the Fin, then this is where it will go – and if you haven’t, now’s the time to register so that your name can travel at 1000 mph!
The front chassis ‘buck’ (the male mould) is now being ‘blocked up’ by UMECO. This is a very apt term for the process – the buck is literally build up from tooling blocks and then machined down to the shape of the front of the Car, so that the carbon fibre female mould can be produced.
Idea (above)....
....and reality
For this lower section (the smaller of the 2 pieces, UMECO will use one tonne of tooling block, with machining taking 8 day shifts and 8 night shifts, after which it will be hand finished and fettled for a further 2 days before being sealed. Then the layup of the carbon tool will then begin. This is not a quick or simple process – but the final result will be one of the strongest cockpits in the world, so it’s worth waiting for.
Getting BLOODHOUND up to speed is only half of the problem – stopping it from 1000 mph is also a top priority...not just for reasons of self-preservation, but also because pulling up at exactly the right spot will shave vital seconds off the Car turnaround time between the two record attempt runs, which have to be completed within an hour.
The Car will be fitted with airbrakes, parachutes and wheel brakes, to give me a range of options for stopping 6 tonnes doing 1000 mph – it’s a big task. The airbrake design has now been brought to life in a video animation, while SES is making our high-speed drag chutes, and Brian Coombs has been finalising the wheel brakes. The desert brakes need to survive the 10,200 RPM spin speed of a 1000 mph run, so the discs will be made from steel. However, for the UK runway tests, we need to stop the Car much more quickly (i.e. before the end of the runway), so we will be using more powerful brakes for the UK runs.
Tight packaging...
...and clever uprights
Brian has been working with AP Racing to produce these runways brakes, which will be carbon/carbon. Unusually, one half of the calliper (the fixed part of the brake) will be built into the upright (the suspension casting that carries the wheel hub).
This is a neat way to keep the package as small as possible – after all, Brian has to fit in 2 wheels, 2 uprights with 2 sets of bearings, 2 brake packs and 2 sets of double wishbone suspension into the nose of the Car – so it’s pretty tight in there.
Finally, I’ve had a chance to do some driver training in preparation for driving BLOODHOUND next year. Radical sportscars has offered us the use of one of their cars, beautifully done up in BLOODHOUND colours, for the occasional track day and race, so that I can improve my car handling skills. (See the picture at the top of the page)
As it’s a 2-seat car, I can also share the experience with the occasional journalist, and perhaps even a few members of our 1K Supporters Club, to explain what I’m practising in preparation for a 1000 mph. Meanwhile, I’ve just finished my first race weekend and the car is still in one piece! I also learned a lot in this amazing race car, and had some fun as the ‘new boy’ at the track.
More pictures and video (including how to go from 200 kmh to facing backwards in 2 seconds – eek!) next month. Meanwhile, we’ll be at the Goodwood Festival of Speed from 28 June to 1 July, with the Radical on show alongside our full-size Show Car, so please come along and see us.