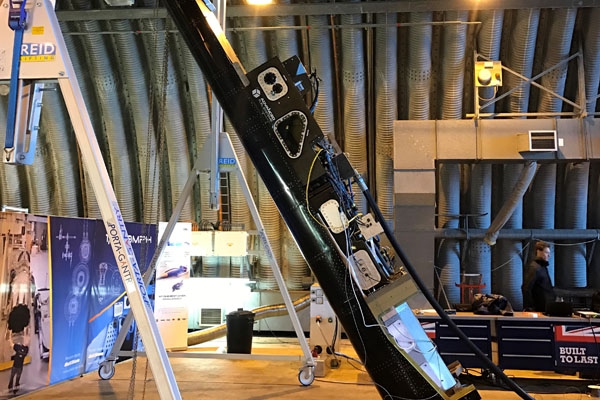
It’s been an interesting start to the New Year, with various bits of the Car being tested as we slowly get BLOODHOUND SSC ready to run. We’ve still got a long way to go, but it’s terrific to see systems being assembled for final installation in the most advanced straight-line racing car ever.
Last month, a small number of the team went down to Newquay Aerohub to test the jet engine’s fuel system (you can watch the latest BHTV video of the test here). Sounds like an easy task – surely all we need to do is check that we can pump the fuel into the Rolls-Royce EJ200 jet engine quickly enough?
Unfortunately it’s not that simple and we have to check a lot more than just maximum flow rate. For example, the fuel has to be pumped into the engine under 2‘G’ acceleration. When I throttle back at 1000 mph, the Car will slow down at 3G, and we want to keep the engine running to help it cool down after the Car comes to a stop.
Heat management is going to be a significant part of getting to 1000 mph safely (I’ll talk more about that another time). Part of the problem is that jet engines create a lot of heat: the ‘turbine inlet temperature’ inside the jet is over 1500 deg C at full power (hotter than molten lava in a volcano). The jet engine sits directly below the base of the Fin (with your name on it? If not, click here). The Fin is aluminium, so we want to avoid excess heat, which could weaken the structure. Giving the jet engine a couple of minutes to cool down at idle power, after a supersonic run, will help to control the heat build-up in the rear of the Car.
To replicate the effects of G for the fuel test, the team built a rig to tilt the whole fuel system to 60 degrees nose-up (to simulate 2G acceleration) (see the picture above) and 70 degrees nose down (simulating 3G deceleration). Under all loads, fuel is pumped from the main fuel tank by a high-volume aircraft pump (rescued from a scrap ex-RAF Tornado). This pump runs on 3-phase alternating current (AC) generated through the EJ200’s ‘aircraft mounted accessory drive’, or AMAD (more of which later).
Slightly thirsty performance
The main fuel tank (400 litres) is constantly ‘topped up’ by 2 auxiliary tanks (100 litres each) after engine start, so that the main tank is still full when I let the brakes off a few minutes after start. The transfer pumps are smaller than the main AC pump (they come from the same scrap Tornado) and run on direct current (DC) from the Car’s 24V DC power system. We need to test both the main tank AC pump and the DC transfer pumps.
There’s more. The EJ200 is a very high performance jet engine (it’s one of the things that makes the RAF’s Typhoon aircraft a world-beater), but at full power it still uses a fair bit of fuel. I can’t tell you exactly how much, as Rolls-Royce doesn’t publish that kind of information, but Wikipedia suggests a figure of 47 grammes/kilo-Newton/second.
This figure is fairly useless, so let’s develop it a bit. If it takes 47g of fuel to produce one kN of thrust for one second, then at the max power of 90kN, the jet will use 90 x 47g (=4230g, or 4.23kg) of fuel per second. Jet fuel is only about 80% of the density of water, so 4.23kg equals about 5.3 litres of fuel per second at full power – that’s enough to empty a standard household bucket in under 2 seconds. Like I said, it’s quite a lot of fuel. Fortunately, BLOODHOUND will get from a standing start to 1000 mph in less than 1 minute, so the 400 litres in the main tank is more than enough to get the job done.
The problem with pumping 5 litres/second of fuel out of the tank is that you’ve got to replace it with something, otherwise the tank collapses. Each fuel tank has an air vent, which allows air into the tank to replace the fuel. This vent system needs to work at high acceleration and deceleration, and not leak!
Watching the fuel
Finally, the World Land Speed Record requires 2 runs in opposite directions within one hour. This is not that difficult to achieve, provided you design the Car to do the ‘turn-round’ servicing fairly quickly between the runs. This includes a quick refuel (ideally less than 10 minutes), so we need to check this as well. For the test programme, we replaced one of the access panels with a clear plastic window, which I found fascinating. I’ve been lucky enough to spend a career flying supersonic jet fighters, but I’ve never seen the fuel in the tanks before. You can watch the tank filling up in this short video clip.
So how did the fuel system get on? Overall, really well. There are just a few small changes that will make the system more reliable. For example, the DC transfer pumps are slightly more powerful than we expected, producing an over-pressure (about half a Bar) in the main tank. To avoid any risk of damaging the tank over time, we will fit a simple return fuel line, balancing up the pressures. The air vent pipe also turned out to be slightly too narrow, causing a small dip in air pressure at maximum flow rate. A small increase in the size of the air breather will ensure good air flow (and fuel flow) throughout the run. Success – the fuel system is pretty much ready to go.
Taking it for a spin
All we need to do now is connect the jet engine and fire it up! OK, it’s not quite that simple. The cockpit controls need to be connected and tested, which is an ongoing process. We also need to be able to spin the jet engine to get it going. The jet’s ‘starter motor’ is a high-speed air turbine (a mere 57,700 revs/minute), which connects to the engine’s ‘AMAD’ gearbox that I mentioned earlier. As I write, the AMAD gearbox and starter motor are being connected up and tested on the Car.
As well as providing a jet engine start capability, spinning up the AMAD also drives the AC generator (the power supply to the AC fuel pump), the DC generator (DC power for the whole Car), and the hydraulic pump (hydraulic power for the airbrakes and winglets). Spinning up a gearbox may not look like much, but we get to test a whole lot of Car systems when we do, so it’s an exciting moment for us. Then it really will be time for me to jump in and fire it up. Can’t wait.
Loads of elephants
While we are getting ready to run the Car for the first time, we’re producing a series of short videos called ‘Anatomy of the Car’. Each episode looks at a different bit of BLOODHOUND SSC, starting at the front and working back. The first episode is, predictably, called ‘The Nose’, and some of the numbers in the video are quite surprising. At maximum speed, the aerodynamic load peaks at a calculated 138,000 Pascals (= Newtons/sq metre). That’s the equivalent load to 2 fully-grown elephants…. and that’s just for the nose cone. Still, the structure is very strong, so I’m not worried by this. I’m more concerned about the calculated figure for aerodynamic heating, which suggests a possible maximum of 134 deg C – which would soften the carbon fibre nose cone – which is sitting under 2 large elephants…..
In reality, the nose should not get anywhere near that temperature, as conduction through the structure, and convection through the air, will remove a lot of the heat (I hope). I suspect that ‘Anatomy of the Car’ is likely to show up a lot of other big (and possibly scary) numbers as it works back along the Car. It’s easy to see why we need over 500 data sensors on a Car that’s hoping to travel at over 1000 mph.
Rockets make the best education
The BLOODHOUND Education Team is still working hard to share the excitement of our 1000 mph ‘Engineering Adventure’ with the largest possible audience. They had a great time last week at the ‘Bett Show’ in London, telling a huge number of young people about the Car, and letting them have a go at their own rocket cars as part of the ‘Race for the Line’ campaign. It clearly had an impact, as the students voted BLOODHOUND best stand at the show. Well done the Education Team.
The shrinking wet patch
While it’s winter here in the UK, it’s the height of summer in South Africa, which is also peak rainy season in the Northern Cape (they get convective rain – thunderstorms, etc. – in the summer and virtually no rain in the winter). We were delighted to see a lot of rain falling around our Hakskeen Pan track last month, flooding a large area, which helps to improve the consistency and smoothness of the track surface each time it floods.
Thanks to our friends at DMC (and their most excellent satellite photos), we can see that the summer heat is already drying the track out, with the ‘wet patch’ now limited to the northern end, along the main tarmac road.
This also illustrates how valuable satellite overviews are for us. The view from the road (which is the only easy way to get to the track) is all water, giving the impression that the whole pan is flooded. From the overhead view, it’s a very different story. The world’s best straight-line race track is getting ready for BLOODHOUND SSC.