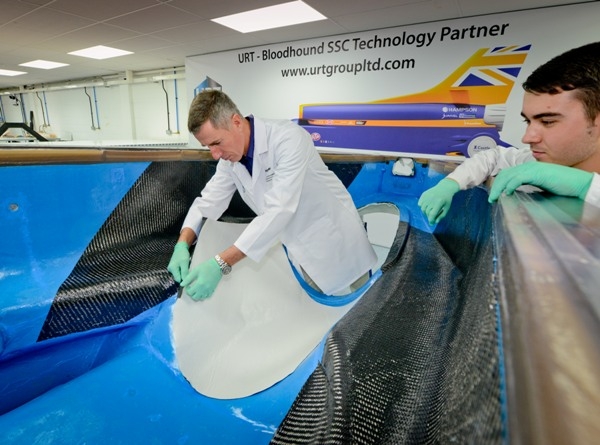
Happy New Year – I hope your New Year has started off as well as ours.
One of the great things about working on Bloodhound is that we all share in the ‘Engineering Adventure’. Our long-term aim is to inspire a generation of young people about the magic of science and technology, through the Bloodhound Education Programme (sign up your school here if you haven’t already – it’s free). In the meantime, while they are learning about Bloodhound technology, I get to learn a huge amount about it as well – and it’s fascinating.
Thrust SSC – Supersonic and from Sussex
I’ve just been down to visit URT on the Sussex coast, to see a major piece of the Car in manufacture. This small area of Sussex has an amazing link with speed the world’s fastest car, Thrust SSC, was created here in the 1990s, the body of the fastest-ever diesel car, the JCB Dieselmax, was built here. Now we’re back here again for a world-class product that will do 1000 mph. Great Britain really does have wonderful engineering expertise in some unlikely places.
URT is currently racing through the build of our carbon fibre monocoque – the major chassis section from the front wheels to middle of the Car. The word ‘monocoque’ literally means ‘single shell’, and is a thick load-bearing skin which forms both outer surface and chassis in one.
The ‘Single Shell’ Chassis
The monocoque has to carry the cockpit (and me!), the rocket oxidiser tank containing one tonne of hydrogen peroxide, the front suspension and steering sub-assembly, and the jet engine intake. It’s a busy piece of the Car.
The monocoque also has to provide the strength in the centre of our 6 tonne Car (7.5 tonnes with fuel). It will experience aerodynamic loads of up to 12 tonnes per square metre, and have to survive acceleration and deceleration loads of up to 3 ‘G’ (3 times the force of gravity). To picture 3 G, imagine driving at 60 mph – and then stopping dead in one second. That’s a 3 G deceleration. You’ll rapidly realise that the only way to achieve this is to crash into something (don’t try this at home) – and Bloodhound is going to be subjected to this much load on every high-speed run.
Another way to picture the sort of loads that Bloodhound is going to experience is to look at the suspension bearings.
Big Loads – Big Bearings
Our suspension consists of independent double wishbones – in other words, each wheel has its own suspension, which consists of 2 horizontal V-shaped brackets, one above the other, hinged on the side of the Car. This sophisticated suspension will ensure precise control of the Car on the desert: the surface is very smooth, but no surface is perfectly flat and there is no such thing as a small bump at 1000 mph. The wishbones (the V-brackets) move up and down on bearings – except a normal race car bearing is about the size of a marble, while Bloodhound’s is closer to the size of an apple. Big loads, big bearings.
So how does URT make a carbon fibre monocoque to a precise shape and to take all this load? They first produce a ‘buck’ (a solid copy of the final shape), precision-machined from a solid block. They make a mould from this in carbon fibre. The mould is made in 2 halves, upper and lower, so that they can get inside it to make the final parts. The monocoque is about 20 mm thick, with a thick carbon outer skin, a foam core and a inner carbon skin.
URT Experts Hard at Work
The carbon skins are made from multiple layers of carbon fibre sheets impregnated with resin (7 layers for the outer skin, 5 layers for the inner). Each piece of sheet is pre-cut and then laid up in a precise position, with the strands of woven carbon running is different directions for each layer, to give a precise amount of strength in each direction – clever stuff.
When I got there, the outer skin had already been laid up and the ‘cooked’ in an autoclave (a very large oven) at up to 10 Bar (150 psi) and 135 deg C. They were kind enough to let the new boy have a go (see the picture at the top of this page), so I got to add a layer of carbon fibre to the inner skin of the monocoque. A big thank you to Josh Cox at URT for his help and patience while I made it look difficult!
Once all 5 layers of inner skin have been added, the upper and lower moulds will be joined for the first time. Then whole thing goes back into the autoclave for another cure, before final machining – and we should get the finished product in a couple of months or so. Can’t wait to see it...
While the final cockpit and monocoque is being made in carbon fibre, we’ve used the fibreglass ‘splash’ to develop the cockpit mock-up. While the 3D computer design is very detailed, I need to sit in the cockpit (or in this case an exact copy) to confirm the exact position of the seat, steering wheel, pedals, etc.
Cockpit Details
We can then fix the exact position of the instrument panels the rest of the controls in the cockpit. By the time the final carbon fibre piece arrives from URT, we should be able to pull the internal fittings out of the mock-up and fix them straight into the cockpit, saving us a lot of time later on. I have to admit that each time I get into the cockpit mock-up and imagine the finished version, I get a quiet thrill. This is going to be a remarkable vehicle.
While the chassis is being manufactured, we’re still working on some fine detail. This includes the aerodynamic stability – making sure that the Fin is big enough to keep the Car pointy-end forwards. To do that, we need the aerodynamic centre of the Car to be behind the centre of gravity.
As the various bits of Car are being manufactured, we are continually updating our calculated centre of gravity, so we need to keep checking the stability. At the moment, it’s not quite stable enough at slow speed (below 600 mph). We have a positive ‘yaw static margin’ (the distance between the centre of gravity and the aerodynamic centre) while the Car is accelerating, but the Car’s centre of gravity moves back slightly as we burn off the fuel, and this leaves the Car less stable as it is slowing down. A small increase in the Fin size (perhaps 50 mm at the back edge) should make a big difference – and will also give room for a few more names! Have you put your name on the Fin yet?
After the recent wheel test in South Africa, Ron Ayers has been analysing the results. Based on the data that he collected, we can make the V-shaped keels much shallower, or even remove the V-keel altogether and use a rounded profile. This will reduce the depth of the wheel track and reduce the risk of damaging the wheel surface on buried stones. We’ve got about 2 months to make the final decision, as the forging of the wheels is being done in March, before the final machining in May.
Wheel Testing in S Africa
Something as apparently simple as making the wheels shows just how many companies are involved in a world-class engineering project like Bloodhound. The lead contractor for the wheel programme is Castle Precision Engineering in Glasgow, with design and analysis support from Innovaltec and Lockheed Martin (UK). Plate aluminium is being supplied by Metal Web, while Raw liquid aluminium (for the forgings) comes from Trimet. Otto Fuchs will carry out the forging, after which the wheels are shot peened. Wikipedia defines shot-peening as ‘a cold working process used to produce a compressive residual stress layer and modify mechanical properties of metals’. What that means in English is blasting the surface with thousands of tiny lumps of ‘shot’ to relieve surface stresses. There’s a lot of stress in a 1000 mph wheel, so anything we can relieve in advance is good. Metal Improvement Company will complete the shot peening, before Amfin carries out non-destructive testing and finally WDB will balance the wheels. There’s a lot to do just to make the wheels, never mind building the rest of the Car to sit on them. 2013 is going to be quite a year – I can’t wait!