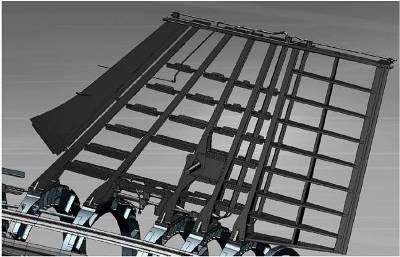
As a Royal Air Force Fighter Pilot, I like to think that I’ve got a reasonable understanding of aircraft and how they work. However, the more time I spend on Bloodhound, the more I learn about just how amazing airplanes, and fast jets in particular, really are. Bloodhound SSC is aiming to do over 1000 mph, which is faster than any aircraft – even the Royal Air Force’s latest Typhoon fighter – can travel at ground level. If we’re going to go that fast, then we’ve got to do this better than any aeroplane, and that’s a huge task.
My learning experience for this month has come from the planning around building the Fin of Bloodhound SSC (pictured above). I thought it would be fairly simple: decide how big the Fin needs to be (we’ve done that), design and stress the internal structure to make sure it will be strong enough (we’ve done that as well) and then just build it. But of course it’s not that easy – there is no such thing as ‘just build it’ when you’re making parts for a 1000 mph Car. The Bloodhound Engineers have been to talk to BAe Systems, as the UK’s leading experts on building fast jets, to discuss how best to build our Fin. There is a good comparison here between the Bloodhound Fin and the fin of the Hawk fast jet trainer, which are both of a similar size. I know the Hawk well, having spent many hours flying it, and it has been made famous as the aircraft used by the Red Arrows. Of course, there are 2 big differences between the Hawk and Bloodhound fins – the Hawk can’t do 1000 mph, and you can’t put your name on the fin of a Red Arrow (whereas you can send your name to 1000 mph on the tail of Bloodhound SSC!). So what can we learn from the people that build the Hawk’s fin?
Famous fins
There are 3 things that can go wrong during the build, and all of them involve the fin not being straight. The shape of the fin may have uneven ‘wobbles’ in it, but that’s not a major problem for Bloodhound. The fin may come out slightly ‘banana’ shaped, which is more of a problem – or it could be twisted from base to tip, which is a big problem. And of course we are only making the one, so we need to get this exactly right first time. How straight does the Fin need to be? We’re aiming for a maximum of 5’ (just under 1/10 of a degree) accuracy between the top and bottom of the Fin. Assuming that the front is perfectly straight (and it should be – it will be a machined from solid metal) then the back of the Fin needs to be accurate to within about 2 mm from top to bottom. To put it more simply – it needs to VERY straight if it’s going to keep the Car pointing in the right direction at 1000 mph.
This is where the advice from the BAe team is so useful. There are several ways to build the Bloodhound Fin. We could assemble the internal structure in a frame, carefull mesaure and fix the structure in place, and then put the skins on both sides, working from the centre outwards. Alternatively, we could fix the internal structure on one side only, then put the skin on the other side, or (best of all – but most expensive) we could build it slightly over-sized, fix it in place and then machine it precisely to shape before adding the skins. Now that we’ve got the options, and an idea of how much time, money and manpower each method will take, the team can agree a plan. Meanwhile, of course, I’m still expecting them to ‘just build it’.
Almost ready for me to move in....
Great news from the team at URT Group, who have now finished the carbon fibre monocoque, which looks just fantastic. Once the final machining has been completed, we’ll take delivery of this key piece of chassis, which really is the centre of the Car.
We can then start to fit out the cockpit as my 1000 mph office, which I’m really looking forward to – after years of discussing ideas, we’re finally getting to make them come true. Of course, that doesn’t mean time off for the URT team, as we’ve got plenty of other carbon fibre bits for them to get cracking on. There’s still the whole of the nose to make!
The aerodynamics team are still working hard, testing the latest refinements to the Car, so that we know what to expect in terms of drag and stability. We’re also doing some more detailed work on the jet intake for the EJ200 engine, as we need to know how fast I can accelerate the engine at the start of the run, and how the intake flow will affect the engine power (and the Car’s handling) at high speeds. Separately, Dr Ben Evans and his team are analysing the stability of the Car with the airbrakes partly deployed, for 2 reasons.
Slowing down the Bloodhound
Firstly, when I deploy the airbrakes, we need to be sure that the Car won’t become unstable (it would be a real problem if I couldn’t slow down!). We’re confident that the stability will increase as the airbrakes come out, but we’d like some hard evidence to confirm that. The second reason is that, once we’ve confirmed that the airbrakes increase the stability of the Car when they are slightly out, we could (if needed) use the airbrakes to stabilise the Car until it goes supersonic. As if there isn’t enough already happening in the cockpit, I may need to blip the airbrakes out very slightly (perhaps 10 degrees) until about 600-700 mph to improve the handling…. or I may not, but it’s nice to know I’ve got the option if I want it.
Runway wheels by Castle Engineering
The wheel development programme is also making good progress. Thanks to the great support from Castle Engineering, we now have our set of runway test wheels, which we’ll be using in the UK later on this year. Following last year’s desert wheel testing, and some more analysis of the results, we’ve decided to conduct a second set of tests. This time, the wheel profiles will be a shallow rounded shape (and with 2 wheels, we can test 2 different profiles). This will give us a range of figures for the depth that the wheels penetrate the desert, and also how much sideways grip they generate.
Choosing a shallow profile will minimise the chances of damaging the wheels on stones buried under the surface, so we’re looking for a very shallow profile with just enough sideways grip. To give you some idea of just how hard the desert is, each wheel will be supporting a load of nearly 2 tonnes. From our desert wheel tests, our performance expert Ron Ayers has come up with a figure for the hardness of Hakskeen Pan.
The desert hardness is (and here’s a figure you will never use in a pub quiz!) about 400 cubic mm per kiloNewton. That means that the wheels only penetrate about 10 mm into the surface, even under 2 tonnes of load. Or put another way, the 2 tonne (20 kN) load only displaces about 8000 cubic mm of desert soil – about a fifth of the volume of a golf ball!
This is a very firm surface by anybody’s standards. Now that the Northern Cape team is finishing up the clearance work, it really is the world’s best race track, just waiting for the world’s first 1000 mph Car to arrive. We’ll be there soon enough….