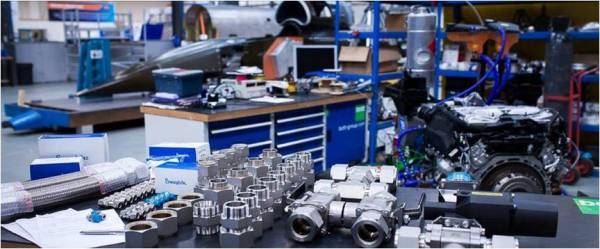
A fascinating thing about prototype engineering projects in general, and Land Speed Records in particular, is how they appear to move forwards in fits and starts. Right now, BLOODHOUND is charging ahead towards completion of the Car this summer, but there are still a few minor ‘speed bumps’ to deal with. The trick is to recognise these bumps for what they are: a perfectly normal part of the ‘Engineering Adventure’ to build the world’s first 1000 mph Car. Fortunately, the speed bumps remain few and far between, so we’re taking them in our stride and still smiling.
Terrific progress has been made over the past few weeks on assembling BLOODHOUND’s Fin (have you put your name on the Fin yet?). This huge structure is days from being completed after an impressive burst of activity. I’m proud to say that the RAF has made this happen, as the Fin has been built by a small and highly skilled team from 71 Squadron, the RAF’s aircraft repair specialists. They’ve got a unique chance to practice and develop their repair and fabrication skills and, as you can imagine, they are loving every moment.

At 1000 mph, BLOODHOUND will be travelling faster than any jet fighter has ever been at ground level (yes, even faster than the remarkable Eurofighter Typhoon). This makes BLOODHOUND’s Fin the hardest working aerodynamic fin ever.
The front and rear edges of the Fin need to line up to within 2mm or less, and the whole structure is stressed to survive side loads of over 5 tonnes. All this strength and accuracy needs to be produced from a kit of 139 precision parts held together by 5000 rivets.

The challenge doesn’t end there. The metal skins for the Fin have ‘compound’ curves (they curve in 2 different directions), so the huge panels need ‘wheeling’ by hand to produce the right curvature, before hand-trimming. Then the drilling-off starts, by hand, which is an epic job. Each hole is created by back-drilling through the relevant rib with a ‘pilot drill’ (that’s a small diameter drill, not an aeroplane checklist). The hole is initially widened to line it up and finally drilled off to the finished size. Then the hole is counter-sunk, to create a shallow depression around the hole for the rivet head, before de-burring (removing any stray slivers of metal) completes the task. That’s 4 different precision hand-drilling tasks for each hole – and there are 5000 of them on the Fin alone.
I don’t know where the 71 Squadron team gets its patience, but I don’t think I could do this job. Fortunately for me, I don’t have to. They are all over this task, delivering world-class work to finish off not only the Fin, but also the equally complex titanium floor that protects the underside of the Car. Hurray for the Royal Air Force!

While the bodywork and Fin are going brilliantly, the rocket system has supplied one of this month’s minor speed bumps. After a previous rear bearing failure in the rocket’s HTP pump, we went back to Newquay to prove that the new test rig had cured the problem. It hadn’t. The bearing failed again.

This failure was even more impressive, with the rear pump bearing completely destroyed, taking out the impeller as well. This was obviously not just a test rig problem. The team quickly found the answer: re-calculating the bearing loads showed that we needed stronger bearings, simple as that. On the plus side, the bearing loads are higher partly because the pump is working better and pumping harder than we had originally expected, which is a good problem to have.
Looking ahead, the bearing failure means that the rocket will not be ready in time for our UK test programme in August. However, Nammo is doing everything it can to help us, so we should still have time to get the rocket system ready for a punt at 800 mph in South Africa in October. The timescale is very tight, but if this was easy, everyone would be doing it….

On the plus side, we’ve already got a full range of Swagelok connectors to bolt the rocket system together. High-quality components are a critical part of assembling so much of BLOODHOUND, particularly the really ‘exciting’ (or scary) bits like the rocket system. It’s another reminder of just what a huge team effort this ‘Engineering Adventure’ really is. A football stadium’s worth of highly skilled people, spread across the UK (and around the world), all helping to build the world’s first 1000 mph car. I love the thought.

Thanks to the terrific support of some 300 sponsor companies, lots of other bits of Car are rapidly coming together. The suspension assemblies are mostly done, and the first brake parachute cans have been delivered. These ‘inner’ chute cans each contain a brake parachute, and to load a fresh chute we just slide the old (empty) can out and slide the new (packed) one in, simple as that.

The airbrake door moulds are now complete and the door themselves are about be produced, along with the wheel fairings for both front and rear wheels. We’ve even started planning slots for the paint bay, to get the Car ready for the outside world, which is a real indication of how far through the build we are now.
I was excited to try the URT/SHD/Sigmatex carbon driver’s seat for the first time this month. The good news (as you would expect from a precision-moulded seat) is that it fits me perfectly. The not-quite-so-good news is that the seat harness routeing isn’t quite where we’d hoped. This is almost inevitable: the carbon fibre cockpit monocoque had to be designed and manufactured about 3 years ago (including the attachment points for my seat harness), and my seating position has changed very slightly, now that the rest of the cockpit is complete.
Fortunately for us, we are working closely with the FIA Institute, who are giving us world-class advice on how to resolve these and other minor snags with the cockpit and safety systems. A change in the layout of the harness lap straps, together with a change to a Simpson hybrid ‘HANS’ (head and neck restraint system), should solve the problems. Another minor speed bump crested on the way to 1000 mph.